A kind of magnesium slag granulation method
A magnesium slag and granulation technology, which is applied in the field of resource utilization of solid waste, can solve the problems of increasing the cost of resource utilization of magnesium slag and difficulty in industrial application, and achieves the goals of promoting utilization and recycling, improving mineralization, and low cost Effect
- Summary
- Abstract
- Description
- Claims
- Application Information
AI Technical Summary
Problems solved by technology
Method used
Examples
Embodiment 1
[0018] A method for granulating magnesium slag, comprising the steps of:
[0019] Step 1: Mix waste glass and borax at a mass ratio of 20:1, then crush and ball-mill the mixture to obtain a magnesium slag optimizer with a fineness of 45 μm and a sieve residue of less than 15%;
[0020] The second step: use calcined dolomite, ferrosilicon reducing agent and mineralizer as raw materials for producing magnesium metal, add magnesium slag optimization agent to the crushed raw materials for producing magnesium metal and mix them uniformly to form a mixture; wherein, in the mixture The mass content of each substance is respectively: 75% of calcined dolomite, 15% of ferrosilicon reducing agent, 0.3% of fluorite (mineralizing agent), and the balance is magnesium slag optimizing agent.
[0021] The third step: put the mixed material (pressed into balls) in the reduction tank, and carry out magnesium smelting according to the Pidgeon method. During the magnesium smelting process, metal m...
Embodiment 2
[0024] A method for granulating magnesium slag, comprising the steps of:
[0025] Step 1: Mix waste glass and borax at a mass ratio of 30:1, then crush and ball-mill the mixture to obtain a magnesium slag optimizer with a fineness of 45 μm and a sieve residue of less than 15%;
[0026] The second step: use calcined dolomite, ferrosilicon reducing agent and mineralizer as raw materials for producing magnesium metal, add magnesium slag optimization agent to the crushed raw materials for producing magnesium metal and mix them uniformly to form a mixture; wherein, in the mixture The mass content of each substance is respectively: 75% of calcined dolomite, 15% of ferrosilicon reducing agent, 0.3% of fluorite (mineralizing agent), and the balance is magnesium slag optimizing agent.
[0027] The third step: put the mixed material (pressed into balls) in the reduction tank, and carry out magnesium smelting according to the Pidgeon method. During the magnesium smelting process, metal m...
Embodiment 3
[0030] A method for granulating magnesium slag, comprising the steps of:
[0031] Step 1: Mix waste glass and borax at a mass ratio of 40:1, then crush and ball-mill the mixture to obtain a magnesium slag optimizer with a fineness of 45 μm and a sieve residue of less than 15%;
[0032] The second step: use calcined dolomite, ferrosilicon reducing agent and mineralizer as raw materials for producing magnesium metal, add magnesium slag optimization agent to the crushed raw materials for producing magnesium metal and mix them uniformly to form a mixture; wherein, in the mixture The mass content of each substance is respectively: calcined dolomite 80%, ferrosilicon reducing agent 15.5%, fluorite (mineralizing agent) 0.3%, and the balance is magnesium slag optimizing agent.
[0033] The third step: put the mixed material (pressed into balls) in the reduction tank, and carry out magnesium smelting according to the Pidgeon method. During the magnesium smelting process, metal magnesiu...
PUM
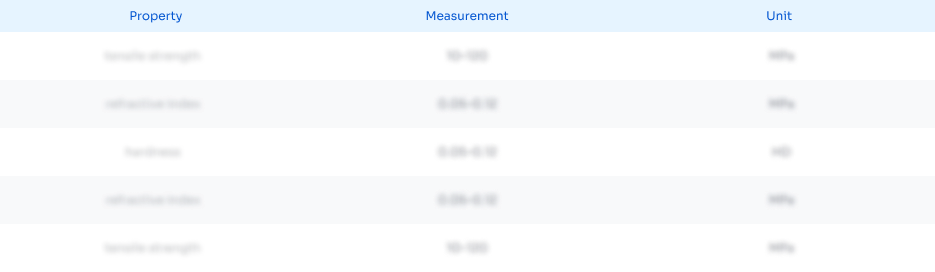
Abstract
Description
Claims
Application Information

- Generate Ideas
- Intellectual Property
- Life Sciences
- Materials
- Tech Scout
- Unparalleled Data Quality
- Higher Quality Content
- 60% Fewer Hallucinations
Browse by: Latest US Patents, China's latest patents, Technical Efficacy Thesaurus, Application Domain, Technology Topic, Popular Technical Reports.
© 2025 PatSnap. All rights reserved.Legal|Privacy policy|Modern Slavery Act Transparency Statement|Sitemap|About US| Contact US: help@patsnap.com