High-speed motor dynamic balance self-adjusting device
A high-speed motor and self-adjusting technology, applied in electromechanical devices, electric components, manufacturing motor generators, etc., can solve problems such as complicated and inaccurate adjustment processes of dynamic balance
- Summary
- Abstract
- Description
- Claims
- Application Information
AI Technical Summary
Problems solved by technology
Method used
Image
Examples
Embodiment 1
[0015] As shown in the figure: the high-speed motor dynamic balance self-adjusting device, including the rotating shaft, counterweight, fixed plate and locking parts, the rotating shaft is connected with the rotating shaft of the motor, and the counterweight is connected to the fixed plate and locked by the locking parts On the rotating shaft, the counterweights are evenly distributed circumferentially around the rotating shaft. The rotating shaft has a dovetail structure, and the fixing plate is provided with a dovetail groove matching the rotating shaft. The counterweight is an annular column structure. Mounting holes are uniformly arranged on the fixed plate
[0016] In this embodiment, the entire breeding device is placed outside the motor, so that the dynamic balance of the entire motor can be adjusted anytime and anywhere. We only need to calculate the weight to be mated during the running and calibration process, and then add and lock the mating we need on the fixed p...
Embodiment 2
[0018] As shown in the figure: the high-speed motor dynamic balance self-adjusting device, including the rotating shaft, counterweight, fixed plate and locking parts, the rotating shaft is connected with the rotating shaft of the motor, and the counterweight is connected to the fixed plate and locked by the locking parts On the rotating shaft, the counterweights are evenly distributed circumferentially around the rotating shaft. The rotating shaft has a dovetail structure, and the fixing plate is provided with a dovetail groove matching the rotating shaft. The counterweight is an arc-shaped block structure. Mounting holes are uniformly arranged on the fixed plate
[0019] During implementation, the entire breeding device is placed outside the motor, so that the dynamic balance of the entire motor can be adjusted anytime and anywhere. We only need to calculate the weight to be mated during the running and calibration process, and then add and lock the mating we need on the fi...
PUM
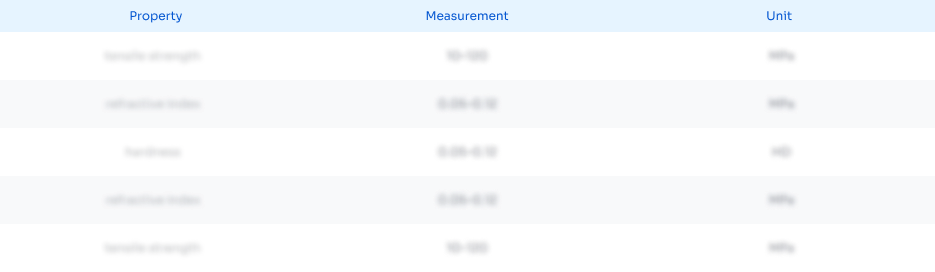
Abstract
Description
Claims
Application Information

- R&D Engineer
- R&D Manager
- IP Professional
- Industry Leading Data Capabilities
- Powerful AI technology
- Patent DNA Extraction
Browse by: Latest US Patents, China's latest patents, Technical Efficacy Thesaurus, Application Domain, Technology Topic, Popular Technical Reports.
© 2024 PatSnap. All rights reserved.Legal|Privacy policy|Modern Slavery Act Transparency Statement|Sitemap|About US| Contact US: help@patsnap.com