Square plate process flow for manufacturing reflective mould
A technological process and mold technology, applied in the electrolytic process, electroforming, etc., can solve the problems of easy wear or deformation, and achieve the effect of increasing the number of ions, facilitating peeling, easy cleaning and electroforming
- Summary
- Abstract
- Description
- Claims
- Application Information
AI Technical Summary
Problems solved by technology
Method used
Examples
Embodiment Construction
[0014] A process flow of a square plate for making a reflective mold, which is characterized in that the process flow is used to make a reflective mold, and the steps are as follows:
[0015] (1) Original plate treatment: Use nickel rod as anode, square metal original plate as cathode, shield and seal the circumference of the original metal plate with tape, leave a blank space of the required size and shape, and fix it on the insulation by bolts On board
[0016] (2) Cleaning and passivation: lye cleaning and passivation are performed on the blank area of the original metal plate. The lye cleaning is to wash the surface of the original metal plate with 8wt%-10wt% sodium hydroxide solution to remove the surface. Oil stains and other impurities are then cleaned with clean water; the passivation treatment is to immerse the original metal plate and the insulating plate fixed with it in a 0.5wt%-1wt% potassium dichromate solution, the temperature is controlled at 35-42 degrees Celsius...
PUM
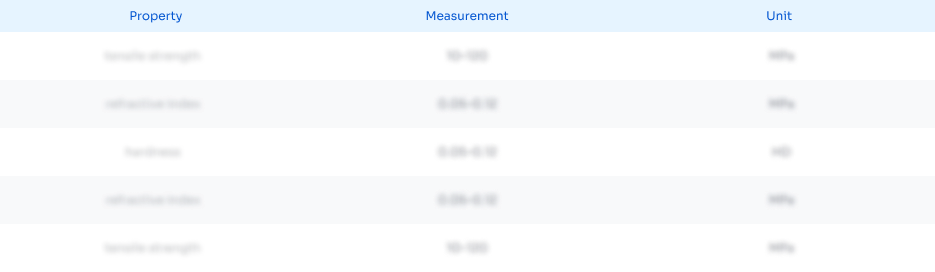
Abstract
Description
Claims
Application Information

- Generate Ideas
- Intellectual Property
- Life Sciences
- Materials
- Tech Scout
- Unparalleled Data Quality
- Higher Quality Content
- 60% Fewer Hallucinations
Browse by: Latest US Patents, China's latest patents, Technical Efficacy Thesaurus, Application Domain, Technology Topic, Popular Technical Reports.
© 2025 PatSnap. All rights reserved.Legal|Privacy policy|Modern Slavery Act Transparency Statement|Sitemap|About US| Contact US: help@patsnap.com