Dual-sliding mode control based speed regulating system and method for direct torque of permanent magnet synchronous motor main axis
A permanent magnet synchronous and speed regulating system technology, applied in the direction of control system, direct torque control, general control strategy, etc., can solve problems such as noise and chattering, and the system is difficult to control accurately, and achieve the solution of flux linkage and torque ripple Large, fast dynamic response, fast dynamic response effect
- Summary
- Abstract
- Description
- Claims
- Application Information
AI Technical Summary
Problems solved by technology
Method used
Image
Examples
Embodiment Construction
[0049] In order to make the purpose, technical solutions and advantages of the embodiments of the present invention clearer, the technical solutions in the embodiments of the present invention will be clearly and completely described below in conjunction with the drawings in the embodiments of the present invention. Obviously, the described embodiments It is a part of embodiments of the present invention, but not all embodiments. Based on the embodiments of the present invention, all other embodiments obtained by persons of ordinary skill in the art without creative efforts fall within the protection scope of the present invention.
[0050] combine figure 1 , a permanent magnet synchronous electric spindle direct torque speed regulation system based on double sliding mode control, including a main circuit, a control circuit, and a signal detection circuit.
[0051] The main circuit includes an inverter and a permanent magnet synchronous spindle (PMSS).
[0052] The control c...
PUM
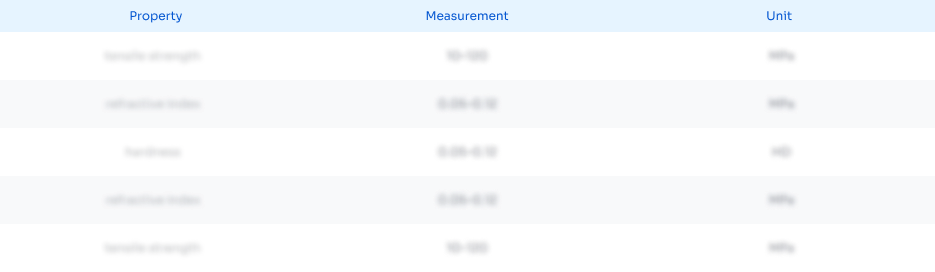
Abstract
Description
Claims
Application Information

- R&D Engineer
- R&D Manager
- IP Professional
- Industry Leading Data Capabilities
- Powerful AI technology
- Patent DNA Extraction
Browse by: Latest US Patents, China's latest patents, Technical Efficacy Thesaurus, Application Domain, Technology Topic, Popular Technical Reports.
© 2024 PatSnap. All rights reserved.Legal|Privacy policy|Modern Slavery Act Transparency Statement|Sitemap|About US| Contact US: help@patsnap.com