Backplate manufacturing method and backplate
A manufacturing method and backplane technology, which are applied in manufacturing tools, ion implantation plating, welding medium, etc., can solve the problems of low strength, poor electrical and thermal conductivity, and the quality of the backplane needs to be improved, so as to improve the quality and improve the welding strength. Effect
- Summary
- Abstract
- Description
- Claims
- Application Information
AI Technical Summary
Problems solved by technology
Method used
Image
Examples
Embodiment Construction
[0042] It can be seen from the background art that the quality of the backplane manufactured in the prior art needs to be improved.
[0043] Now combine with a backplane manufacturing method for analysis. refer to figure 1 , figure 1 It is a schematic diagram of a manufacturing method of a backplane. The stainless steel substrate 100 has a cavity that penetrates up and down. On a section perpendicular to the top surface of the stainless steel substrate 100, the edge of the cavity is stepped; the copper substrate 200 is in the cavity In vivo, the sides of the copper substrate 200 match the cavity. The side of the copper substrate 200 includes a transverse surface 210 and a longitudinal surface 220 , and there is a gap between the longitudinal surface 220 and the cavity, so as to avoid mutual extrusion of the copper substrate 200 and the stainless steel substrate 100 caused by thermal expansion and contraction. During soldering, solder is placed on the lateral surface 210, th...
PUM
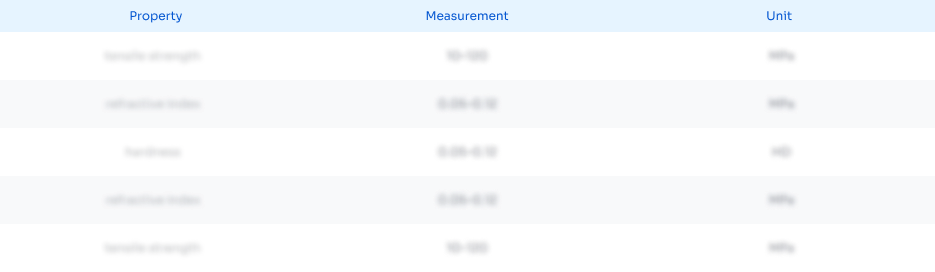
Abstract
Description
Claims
Application Information

- R&D Engineer
- R&D Manager
- IP Professional
- Industry Leading Data Capabilities
- Powerful AI technology
- Patent DNA Extraction
Browse by: Latest US Patents, China's latest patents, Technical Efficacy Thesaurus, Application Domain, Technology Topic, Popular Technical Reports.
© 2024 PatSnap. All rights reserved.Legal|Privacy policy|Modern Slavery Act Transparency Statement|Sitemap|About US| Contact US: help@patsnap.com