High-efficiency machining control method for deep hole in oil pump casing
A control method and oil pump technology, which is applied in the field of mechanical deep hole processing, can solve the problems of weak tool rigidity and low cutting efficiency, optimize the cutting process path, improve processing stability and workpiece surface quality, and perform efficient and stable deep hole processing Effect
- Summary
- Abstract
- Description
- Claims
- Application Information
AI Technical Summary
Problems solved by technology
Method used
Image
Examples
Embodiment Construction
[0045] The present invention will be described in detail below in conjunction with the accompanying drawings and embodiments.
[0046] A high-efficiency machining control method for deep holes in the oil pump housing of the present invention comprises the following steps:
[0047] S1. According to the dynamic equation of the cutting processing system, calculate the modal transfer function H of the cutting processing system 1 (ω,n);
[0048] S2. According to the processing depth, set a row of points evenly spaced from the tip of the tool to the end of the tool bar, a total of k points, which are marked as: 1, 2, 3, ..., k, through the modal test, in order to obtain the The modal (transfer) function of the node, set to H 3i (ω1), i=1, 2, 3, ..., k;
[0049] S3, through the modal transfer function H of the cutting processing system 1 (ω, n) and the modal transfer function of each node of the tool to establish the cutting process transfer function Φ of different nodes of the t...
PUM
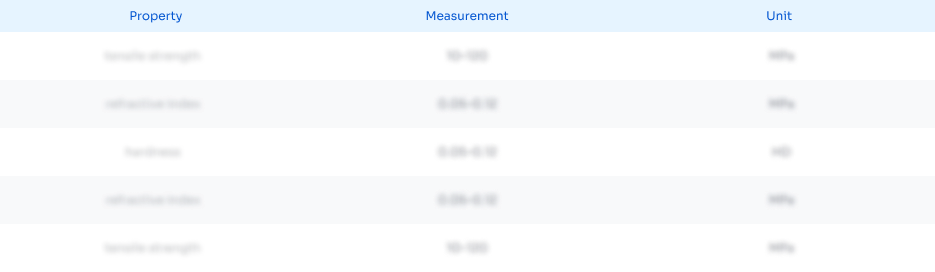
Abstract
Description
Claims
Application Information

- R&D Engineer
- R&D Manager
- IP Professional
- Industry Leading Data Capabilities
- Powerful AI technology
- Patent DNA Extraction
Browse by: Latest US Patents, China's latest patents, Technical Efficacy Thesaurus, Application Domain, Technology Topic, Popular Technical Reports.
© 2024 PatSnap. All rights reserved.Legal|Privacy policy|Modern Slavery Act Transparency Statement|Sitemap|About US| Contact US: help@patsnap.com