Cement clinker preparation method and device
A technology for cement clinker and preparation device, applied in lighting and heating equipment, electric furnace heating, furnace and other directions, can solve the problems of unsatisfactory environmental protection effect and low efficiency, and achieve good ecological environmental benefits, good quality and low power consumption. Effect
- Summary
- Abstract
- Description
- Claims
- Application Information
AI Technical Summary
Problems solved by technology
Method used
Image
Examples
Embodiment 1
[0022] The raw material powder is calcined at 1100°C for 0.5 hours to obtain the embryo, and electrodes are added to the embryo, and then at 1160°C, the electric field strength is 100V / mm, and the current is controlled at 10 mA / mm 2 After 30 seconds of electrification, the cement clinker was rapidly cooled to room temperature. The results of the XRD semi-quantitative test of the clinker mineral crystal content are shown in Table 2:
[0023] Table 2
[0024] C3S%
Embodiment 2
[0026] The raw material powder is calcined at 1200°C for 1 hour to obtain the blank, and electrodes are added on the blank, and then at 1168°C, the electric field strength is 200V / mm, and the current is controlled at 20mA / mm 2 , energized for 300 seconds, cooled to room temperature to obtain cement clinker, XRD semi-quantitative test clinker mineral crystal content results are shown in Table 3:
[0027] table 3
[0028] C3S%
Embodiment 3
[0030] The raw material powder is calcined at 1000°C for 40 minutes to obtain the blank, and electrodes are added to the blank, and then at 1000°C, the electric field strength is 20V / mm, and the current is controlled at 5 mA / mm 2 , energized for 600 seconds and cooled to room temperature to obtain cement clinker, XRD semi-quantitative test clinker mineral crystal content results are shown in Table 4:
[0031] Table 4
[0032] C3S%
PUM
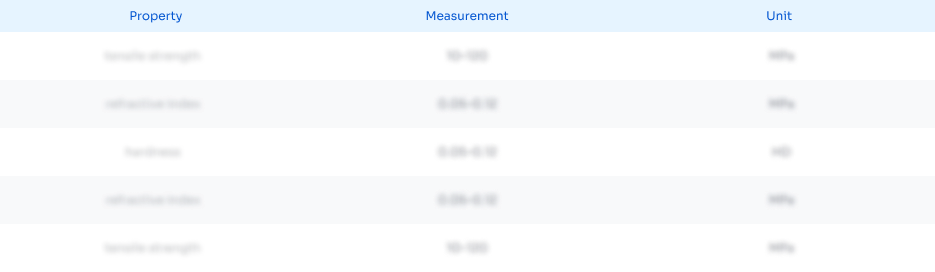
Abstract
Description
Claims
Application Information

- R&D
- Intellectual Property
- Life Sciences
- Materials
- Tech Scout
- Unparalleled Data Quality
- Higher Quality Content
- 60% Fewer Hallucinations
Browse by: Latest US Patents, China's latest patents, Technical Efficacy Thesaurus, Application Domain, Technology Topic, Popular Technical Reports.
© 2025 PatSnap. All rights reserved.Legal|Privacy policy|Modern Slavery Act Transparency Statement|Sitemap|About US| Contact US: help@patsnap.com