Bulkhead sound insulation and thermal insulation composite structure
A composite structure and bulkhead technology, which is applied in sound insulation, building components, building structures, etc., can solve the problems that bulkheads cannot satisfy sound insulation and light weight at the same time, and achieve the effects of increasing rigidity, reducing weight, and blocking heat transmission
- Summary
- Abstract
- Description
- Claims
- Application Information
AI Technical Summary
Problems solved by technology
Method used
Image
Examples
Embodiment 1
[0023] The materials and parameters of each layer are as follows: the first panel 1 and the second panel 7 are both steel plates with a thickness of 0.3mm; the first honeycomb panel 2 and the second honeycomb panel 6 are both aluminum honeycomb panels with a thickness of 5mm and a side length of 5mm; The perforated plate 3 and the second perforated plate 5 are both 0.3 mm thick steel plates, and the perforated shape is a round hole with a diameter of 1.5 mm and a perforation rate of 2%; the heat insulating material layer 4 is a glass wool heat insulating plate with a thickness of 40 mm. Press each layer of boards figure 1 Bonding and compounding were carried out, and the adhesive used conventional commercial adhesives to prepare test samples of the bulkhead composite structure. The sound insulation test was carried out using GB / T 19889.3-2005, and the weighted sound insulation was 36dB.
Embodiment 2
[0025] The materials and parameters of each layer are as follows: the first panel 1 and the second panel 7 are steel plates with a thickness of 0.6mm; the first honeycomb panel 2 and the second honeycomb panel 6 are aluminum honeycomb panels with a thickness of 10mm and a side length of 10mm; the first perforation The plate 3 and the second perforated plate 5 are both 0.3mm thick steel plates, the perforated shape is a round hole, the hole diameter is 2mm, and the perforation rate is 3%; the heat insulation material layer is a 50mm thick mineral wool heat insulation board. Press each layer of boards figure 1 Bonding and compounding are carried out, and the adhesive is conventional commercially available adhesives, and the bulkhead composite structure test sample is prepared, and the sound insulation test is carried out on it according to GB / T 19889.3-2005, and the weighted sound insulation value of the test is 43dB.
Embodiment 3
[0027] The materials and parameters of each layer are as follows: the first panel 1 is a steel plate with a thickness of 2mm; the first honeycomb panel 2 is an aluminum honeycomb panel with a thickness of 10mm and a side length of 10mm; the first perforated plate 3 is a 0.5mm thick steel plate, and the perforation shape is a round hole , aperture 4mm, perforation rate 6%; thermal insulation material layer is 80mm thick mineral wool insulation board, the second perforated plate 5 is 0.3mm thick steel plate, perforation shape is round hole, aperture 3mm, perforation rate 3%; The second honeycomb panel 6 is an aluminum honeycomb panel with a thickness of 10 mm and a side length of 10 mm; the second panel 7 is a steel plate with a thickness of 0.3 mm. Press each layer of boards figure 1 Bonding and compounding were carried out, and the adhesive used conventional commercial adhesives to prepare test samples of the bulkhead composite structure. The sound insulation test was carried ...
PUM
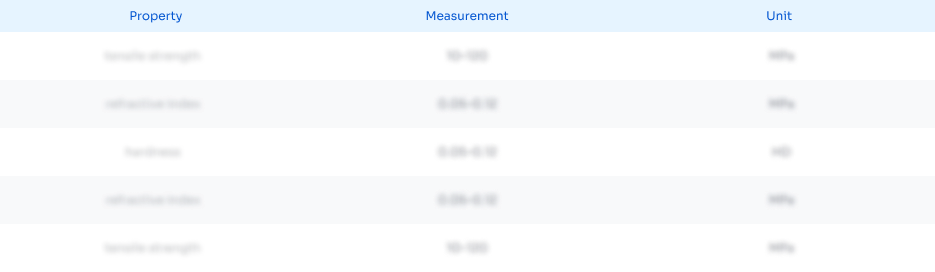
Abstract
Description
Claims
Application Information

- R&D
- Intellectual Property
- Life Sciences
- Materials
- Tech Scout
- Unparalleled Data Quality
- Higher Quality Content
- 60% Fewer Hallucinations
Browse by: Latest US Patents, China's latest patents, Technical Efficacy Thesaurus, Application Domain, Technology Topic, Popular Technical Reports.
© 2025 PatSnap. All rights reserved.Legal|Privacy policy|Modern Slavery Act Transparency Statement|Sitemap|About US| Contact US: help@patsnap.com