Furnace protection process combining high flow bottom blowing slag splashing with top blowing slag splashing
A large flow, slag phase technology, applied in the field of metallurgy, can solve problems such as poor furnace maintenance effect, achieve the effect of shortening the time of slag splashing and furnace protection, shortening the time of furnace protection, and reducing the frequency of static maintenance
- Summary
- Abstract
- Description
- Claims
- Application Information
AI Technical Summary
Problems solved by technology
Method used
Examples
Embodiment 1
[0038] Add lime, limestone, light-burned dolomite, raw dolomite, and magnesite during the smelting process of the converter to obtain the final slag of the converter. After tapping, adjust the nitrogen flow rate of the carrier gas of the bottom blowing lance to 2000Nm 3 / h, annular seam gas nitrogen flow rate to 100Nm 3 / h, blow nitrogen into the furnace, shake the furnace back and forth to splash slag for 1.5min, then lower the top gun to splash slag, adjust the top gun to 200mm above the reference gun position and blow nitrogen into the furnace, the nitrogen flow rate is 28500Nm 3 / h, at the same time, adjust the nitrogen flow rate of the carrier gas of the bottom blowing powder spray gun to 500Nm 3 / h, annular seam gas nitrogen flow rate to 50Nm 3 / h; After this method is used to protect the furnace by slag splashing, the slag hangs evenly in the furnace, and there is no uneven slag hanging in the position of the furnace.
Embodiment 2
[0040] Add lime, limestone, light-burned dolomite, raw dolomite, and magnesite during the smelting process of the converter to obtain the final slag of the converter. After tapping, adjust the nitrogen flow rate of the carrier gas of the bottom blowing lance to 2400Nm 3 / h, annular seam gas nitrogen flow rate to 200Nm 3 / h, blow nitrogen into the furnace, shake the furnace back and forth for 2.5 minutes to splash slag, then lower the top gun to splash slag, adjust the top gun to 600mm above the reference gun position and blow nitrogen into the furnace, the nitrogen flow rate is 31500Nm 3 / h, at the same time, adjust the nitrogen flow rate of the carrier gas of the bottom blowing powder gun to 1000Nm 3 / h, annular seam gas nitrogen flow rate to 100Nm 3 / h; After this method is used to protect the furnace by slag splashing, the slag hangs evenly in the furnace, and there is no uneven slag hanging in the position of the furnace.
Embodiment 3
[0042] Add lime, limestone, light-burned dolomite, raw dolomite, and magnesite during the smelting process of the converter to obtain the final slag of the converter. After tapping, adjust the nitrogen flow rate of the carrier gas of the bottom blowing lance to 2200Nm 3 / h, the annular seam gas nitrogen flow rate to 150Nm 3 / h, blow nitrogen into the furnace, shake the furnace back and forth to splash slag for 2 minutes, then lower the top gun to splash slag, adjust the top gun to 400mm above the reference gun position and blow nitrogen into the furnace, the nitrogen flow rate is 30500Nm 3 / h, at the same time, adjust the nitrogen flow rate of the carrier gas of the bottom blowing powder spray gun to 800Nm 3 / h, annular seam gas nitrogen flow rate to 80Nm 3 / h; After this method is used to protect the furnace by slag splashing, the slag hangs evenly in the furnace, and there is no uneven slag hanging in the position of the furnace.
PUM
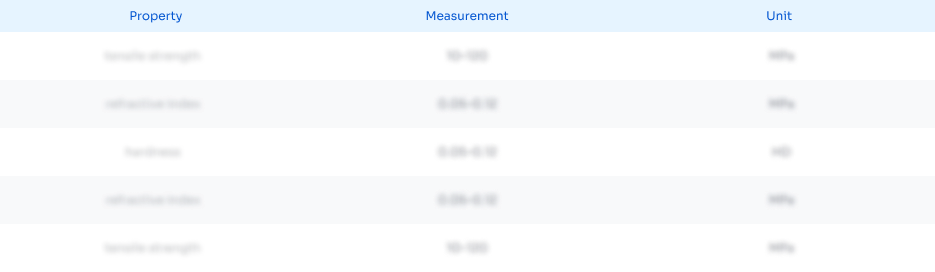
Abstract
Description
Claims
Application Information

- R&D
- Intellectual Property
- Life Sciences
- Materials
- Tech Scout
- Unparalleled Data Quality
- Higher Quality Content
- 60% Fewer Hallucinations
Browse by: Latest US Patents, China's latest patents, Technical Efficacy Thesaurus, Application Domain, Technology Topic, Popular Technical Reports.
© 2025 PatSnap. All rights reserved.Legal|Privacy policy|Modern Slavery Act Transparency Statement|Sitemap|About US| Contact US: help@patsnap.com