Method for preparing high-strength transparent cellulose film material in low-temperature and normal-pressure cooking manner and application thereof
A cellulose film, atmospheric pressure cooking technology, applied in the direction of pressurized wood treatment, wood treatment, wood heating, etc., can solve the problems of fiber damage, poor tensile strength of transparent cellulose materials, and decreased cellulose polymerization degree, etc. Achieve the effect of reducing damage, retaining cellulose polymerization degree and reducing degradation
- Summary
- Abstract
- Description
- Claims
- Application Information
AI Technical Summary
Problems solved by technology
Method used
Examples
Embodiment 1
[0026] (1) cut the fir section into 50mm * 40mm * 1mm wood chips;
[0027] (2) Add wood chips to the cooking solution containing sodium chlorite (0.1g / g, relative to dry wood chips), glacial acetic acid (0.25mL / g, relative to dry wood chips) and deionized water In the beaker, the liquid ratio is 1:30g / mL (wood chip mass: deionized water volume), the cooking temperature is 75°C, and an equal amount of cooking liquid is added every 2 hours (referring to the cooking liquid equal to the amount used for the first time, The same below), cook at normal pressure for 10 hours until the wood chips turn white completely, without stirring during the reaction, to keep the complete shape and structure of the wood chips;
[0028] (3) Washing the cooked wood chips to remove residual cooking liquid;
[0029] (4) Dry the washed wood chips for 10 h under a pressure of 6 MPa to prepare a high-strength transparent cellulose film material.
[0030] The tensile strength of the untreated wood chips...
Embodiment 2
[0032] (1) cut the fir section into 50mm * 40mm * 1mm wood chips;
[0033](2) Add wood chips to the cooking solution containing sodium chlorite (0.3g / g, relative to dry wood chips), glacial acetic acid (0.25mL / g, relative to dry wood chips) and deionized water In a beaker, the liquid ratio is 1:30g / mL (the mass of wood chips: the volume of deionized water), the cooking temperature is 75°C, an equal amount of cooking liquid is added every 2 hours, and the cooking liquid is cooked at normal pressure for 8 hours until the wood chips are completely white. There is no need to stir in order to maintain the complete shape and structure of the wood chips;
[0034] (3) Washing the cooked wood chips to remove residual cooking liquid;
[0035] (4) Dry the washed wood chips for 10 h under a pressure of 6 MPa to prepare a high-strength transparent cellulose film material.
[0036] The tensile strength of the untreated wood chips used in the experiment was 48 MPa, and the fiber polymeriza...
Embodiment 3
[0038] (1) cut the fir section into 50mm * 40mm * 1mm wood chips;
[0039] (2) Add wood chips to the cooking solution containing sodium chlorite (1.0g / g, relative to dry wood chips), glacial acetic acid (0.25mL / g, relative to dry wood chips) and deionized water In a beaker, the liquid ratio is 1:30g / mL (the mass of wood chips: the volume of deionized water), the cooking temperature is 75°C, an equal amount of cooking liquid is added every 2 hours, and the cooking liquid is cooked at normal pressure for 4 hours until the wood chips are completely white. There is no need to stir in order to maintain the complete shape and structure of the wood chips;
[0040] (3) Washing the cooked wood chips to remove residual cooking liquid;
[0041] (4) Dry the washed wood chips for 10 h under a pressure of 6 MPa to prepare a high-strength transparent cellulose film material.
[0042] The tensile strength of the untreated wood chips used in the experiment was 48 MPa, and the fiber polymeriz...
PUM
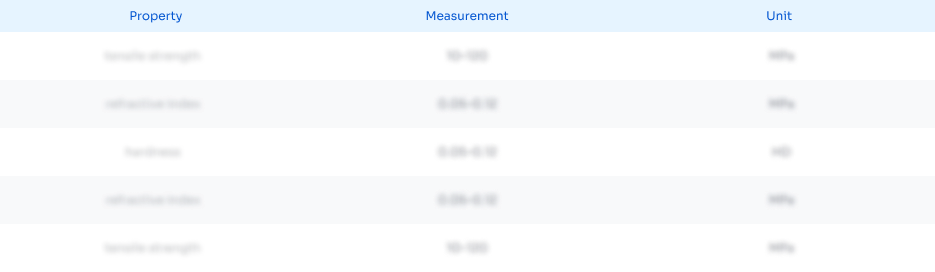
Abstract
Description
Claims
Application Information

- R&D
- Intellectual Property
- Life Sciences
- Materials
- Tech Scout
- Unparalleled Data Quality
- Higher Quality Content
- 60% Fewer Hallucinations
Browse by: Latest US Patents, China's latest patents, Technical Efficacy Thesaurus, Application Domain, Technology Topic, Popular Technical Reports.
© 2025 PatSnap. All rights reserved.Legal|Privacy policy|Modern Slavery Act Transparency Statement|Sitemap|About US| Contact US: help@patsnap.com