Non-contact micro-cantilever beam rigidity measurement method based on electrostatic force
A measurement method, cantilever beam technology, applied in the direction of measuring devices, elastic testing, machine/structural component testing, etc., can solve the problems of uneven distribution of density and Young's modulus, cantilever beam measurement, etc., to avoid errors and the damage to the needle tip, the structure is simple and effective, and the effect of reducing uncertainty
- Summary
- Abstract
- Description
- Claims
- Application Information
AI Technical Summary
Problems solved by technology
Method used
Image
Examples
Embodiment 1
[0062] For example Figure 4a and Figure 4b The stiffness of a gold-coated microcantilever shown as 5 mm long, 0.5 mm wide, and 10 μm thick was measured.
[0063] After capacitance gradient measurement, capacitance gradient constant term A 1 The measured value and the slope k of each fitting line after stiffness fitting are shown in Table 1, and the measured value of stiffness is 0.3775N / m.
[0064] Table 1 capacitance gradient constant item A 1 and the measurement results of the cantilever beam stiffness k
[0065]
PUM
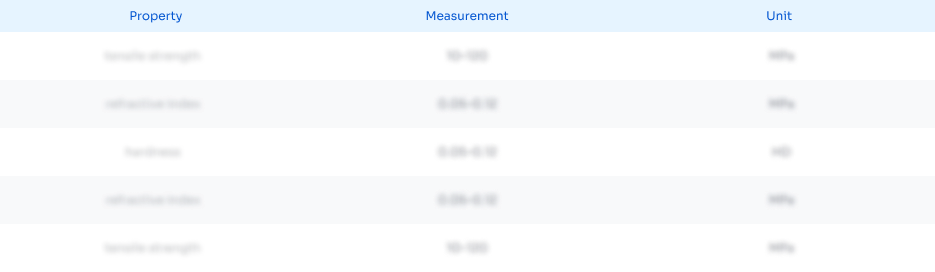
Abstract
Description
Claims
Application Information

- R&D
- Intellectual Property
- Life Sciences
- Materials
- Tech Scout
- Unparalleled Data Quality
- Higher Quality Content
- 60% Fewer Hallucinations
Browse by: Latest US Patents, China's latest patents, Technical Efficacy Thesaurus, Application Domain, Technology Topic, Popular Technical Reports.
© 2025 PatSnap. All rights reserved.Legal|Privacy policy|Modern Slavery Act Transparency Statement|Sitemap|About US| Contact US: help@patsnap.com