Robot hand and eye calibrating method based on scanner
A calibration method and robot hand technology, applied in the direction of manipulators, manufacturing tools, etc., can solve the problems of machining error, debugging error, repeated positioning accuracy and absolute positioning accuracy, etc.
- Summary
- Abstract
- Description
- Claims
- Application Information
AI Technical Summary
Problems solved by technology
Method used
Image
Examples
Embodiment Construction
[0034] The present invention will be further described below in conjunction with drawings and embodiments. It should be understood that the specific embodiments described here are only used to explain the present invention, but not to limit the present invention. In addition, it should be noted that, for the convenience of description, only parts related to the present invention are shown in the drawings but not all content.
[0035] Please refer to figure 1 as shown, figure 1 It is a schematic diagram of the scanner-based robot hand-eye calibration system provided by the present invention, in which 101 is a robot, 102 is a workpiece, 103 is a scanner, and 104 is a base of the robot. There are two types of hand-eye systems depending on where the scanner is installed. One is Eye-in-hand. In this type of hand-eye system, the scanner is fixed at the end of the robot, and the scanner moves with the end of the robot. The vision guidance system is a typical representative of thi...
PUM
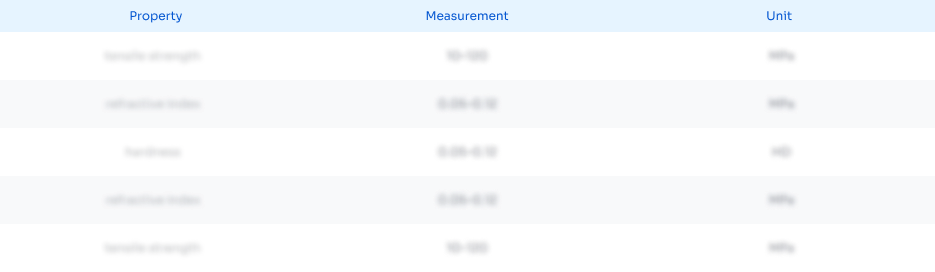
Abstract
Description
Claims
Application Information

- R&D
- Intellectual Property
- Life Sciences
- Materials
- Tech Scout
- Unparalleled Data Quality
- Higher Quality Content
- 60% Fewer Hallucinations
Browse by: Latest US Patents, China's latest patents, Technical Efficacy Thesaurus, Application Domain, Technology Topic, Popular Technical Reports.
© 2025 PatSnap. All rights reserved.Legal|Privacy policy|Modern Slavery Act Transparency Statement|Sitemap|About US| Contact US: help@patsnap.com