A Blast Furnace Top Material Tank Diffuse Gas Full Recovery System and Its Safe Maintenance Method
A technology for releasing gas and gas systems, applied to blast furnaces, blast furnace details, blast furnace parts, etc., to solve problems such as explosions, gas leakage, and oxygen mixing
- Summary
- Abstract
- Description
- Claims
- Application Information
AI Technical Summary
Problems solved by technology
Method used
Image
Examples
Embodiment 1
[0042] A full recovery system for blown gas from the top material tank of a blast furnace, which is used to recover the diffused gas in the material tank. In the stage of gas recovery, the free pressure difference between the diffused gas in material tank 1 and the gas pipeline network 10 is used to directly recover the high-pressure diffused gas in material tank 1 to the gas pipeline network 10; Injection recovery of low-pressure gas. When the full recovery system of the blown gas from the top material tank of the blast furnace breaks down, it can realize safe maintenance.
[0043] see figure 1, the blast furnace top material tank release gas full recovery system includes the first dust collector 2, ejector 3 and second dust collector 4, material tank 1, first dust collector 2, ejector 3, and second dust collector 4 It is communicated with gas pipe network 10 successively by gas pipe, and material tank 1 releases gas outlet gas pipe and installs release valve 52 under the f...
Embodiment 2
[0054] Based on the same inventive concept, this embodiment also provides a full gas recovery system for blast furnace top material tank release gas. low-pressure gas installations. Due to the narrow range of low pressure and improper operation, it is easy to cause excessive ejection, which will cause negative pressure in the material tank and enter the air, thus bringing the risk of explosion to the entire gas recovery system. The full gas recovery system of the blast furnace top tank of the present embodiment can avoid the above-mentioned risks under the condition that the conventional gas recovery function and the safety maintenance function are satisfied.
[0055] see figure 2 , the blast furnace top material tank release gas full recovery system includes the first dust collector 2, ejector 3 and second dust collector 4, material tank 1, first dust collector 2, ejector 3, and second dust collector 4 It communicates with the gas pipe network 10 in turn through the gas pi...
Embodiment 3
[0070] A safety overhaul method for a blast furnace top material tank release gas full recovery system, the blast furnace top material tank full gas recovery system of embodiment 1 or embodiment 2 can be used, and the safety overhaul method includes the following steps:
[0071] (1) The gas replacement process when the system is shut down;
[0072] (1-1) Firstly close the gas recovery valve group (hydraulic valve 55, blind valve 61) of the material tank, then close the valve group (hydraulic valve 58, blind valve 64) connected to the gas pipe network, and then close the pilot Injector injection valve group (hydraulic valve 57, blind valve 62) and the second dust collector inlet blind valve 63, at this time, the entire blast furnace top tank release gas recovery system forms a closed gas system, and is divided into Three sections, including 3 pipe sections of the ejector, 14 pipe sections of the high-pressure gas recovery pipeline and 4 pipe sections of the second dust collecto...
PUM
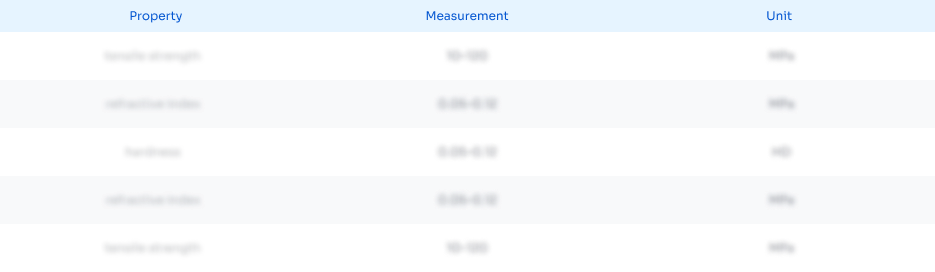
Abstract
Description
Claims
Application Information

- Generate Ideas
- Intellectual Property
- Life Sciences
- Materials
- Tech Scout
- Unparalleled Data Quality
- Higher Quality Content
- 60% Fewer Hallucinations
Browse by: Latest US Patents, China's latest patents, Technical Efficacy Thesaurus, Application Domain, Technology Topic, Popular Technical Reports.
© 2025 PatSnap. All rights reserved.Legal|Privacy policy|Modern Slavery Act Transparency Statement|Sitemap|About US| Contact US: help@patsnap.com