Ink and preparation method thereof
An ink, weight percentage technology, applied in the field of ink and its preparation, can solve the problems of not being able to truly present the product, not accepting signatures, inconsistent base paper, etc., and achieve the effect of strong color stability, preventing floating color and increasing brightness.
- Summary
- Abstract
- Description
- Claims
- Application Information
AI Technical Summary
Problems solved by technology
Method used
Examples
preparation example Construction
[0026] A method for preparing ink, which is characterized in that it comprises the following steps:
[0027] Step 1. Weigh the raw materials according to weight percentages: maleic rosin resin, polyacrylic acid resin and silicon dioxide, add the above raw materials to the reaction kettle in sequence, fully stir at a temperature of 50-60°C, and continue stirring for 60-80 minutes;
[0028] Step 2: Weigh the raw materials: water-based pigments and distilled water according to the weight percentage, and put them into the above reaction kettle, and continue to stir for 60-80 minutes at a temperature of 45-55°C;
[0029] Step 3: Weigh the raw materials according to weight percentage: put the wetting agent, plasticizer, diluent and dispersant into the above-mentioned reaction kettle, and continue to stir for 10-20min at a temperature of 40-50℃;
[0030] Step 4: After completion, let it stand, and finally filter out the material to prepare the ink.
Embodiment 1
[0033] S1. Weigh the raw materials according to the weight percentage: 13% maleic rosin resin, 16% polyacrylic resin and 15% silica. Add the above-mentioned raw materials to the reactor in turn, stir fully at 60°C and continue stirring for 70 minutes ;
[0034] S2: Weigh the raw materials according to weight percentage: 20% of water-based pigment and 23% of distilled water, put them into the above reaction kettle, and continue to stir for 60 minutes at a temperature of 55°C;
[0035] S3. Weigh the raw materials according to weight percentage: 1% glycerin, 3% dioctyl phthalate, 6% water-soluble aldehyde and ketone resin and 3% polyethylene glycol, put them into the above-mentioned reaction kettle at a temperature of 50°C Stir continuously for 20 minutes;
[0036] S4. After completion, let it stand, and finally filter out the material to prepare the ink.
Embodiment 2
[0038] S1, weigh the raw materials according to weight percentage: maleic acid rosin resin 16%, polyacrylic resin 18% and silicon dioxide 14%. Add the above raw materials to the reactor in turn, stir fully at 55°C and continue stirring for 70 minutes ;
[0039] S2: Weigh the raw materials according to weight percentages: 21% of water-based pigments and 20% of distilled water, put them into the above reaction kettle, and continue to stir for 60 minutes at a temperature of 50°C;
[0040] S3. Weigh the raw materials according to the weight percentage: 1% glycerin, 3% dioctyl phthalate, 4% water-soluble aldehyde and ketone resin and 3% polyethylene glycol into the above-mentioned reaction kettle at a temperature of 50°C Stir continuously for 20 minutes;
[0041] S4. After completion, let it stand, and finally filter out the material to prepare the ink.
PUM
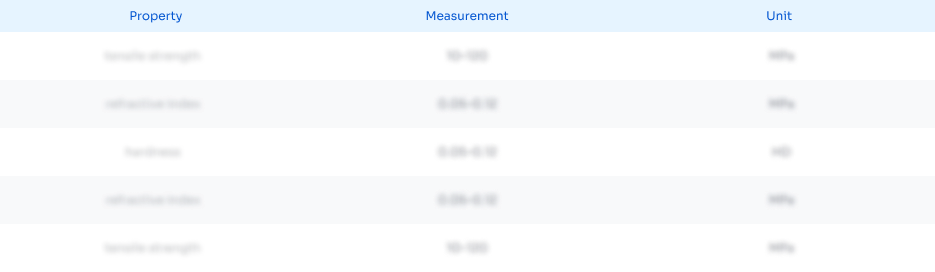
Abstract
Description
Claims
Application Information

- R&D
- Intellectual Property
- Life Sciences
- Materials
- Tech Scout
- Unparalleled Data Quality
- Higher Quality Content
- 60% Fewer Hallucinations
Browse by: Latest US Patents, China's latest patents, Technical Efficacy Thesaurus, Application Domain, Technology Topic, Popular Technical Reports.
© 2025 PatSnap. All rights reserved.Legal|Privacy policy|Modern Slavery Act Transparency Statement|Sitemap|About US| Contact US: help@patsnap.com