Cable-direction-following ROV winch applied to non-power-locating mother ship
A non-power, mother ship technology, applied in the direction of motor vehicles, special purpose ships, ship construction, etc., can solve the problem of huge pulling force of ROV umbilical cables
- Summary
- Abstract
- Description
- Claims
- Application Information
AI Technical Summary
Problems solved by technology
Method used
Image
Examples
Embodiment Construction
[0022] In order to make the above objects, features and advantages of the present invention more comprehensible, the present invention will be further described in detail below in conjunction with the accompanying drawings and specific embodiments.
[0023] Such as figure 1 As shown, a cable direction follower ROV winch applied to a non-dynamically positioned mother ship, including a non-dynamically positioned mother ship 1, an A-frame 2 arranged on the non-dynamically positioned mother ship 1, a winch retracting and releasing cable roller 6, and an underwater robot 3. The pulley 4 is rotatably connected to the A-frame 2, and a positioning piece 5 for guiding the umbilical cable 61 is also fixedly connected to the non-dynamically positioned mother ship 1. The umbilical cable 61 is connected to the underwater robot 3, and the umbilical cable 61 is wound around Over pulley 4 and locator 5 link to each other with winch retractable cable roller 6, and the end portion of A-frame 2 ...
PUM
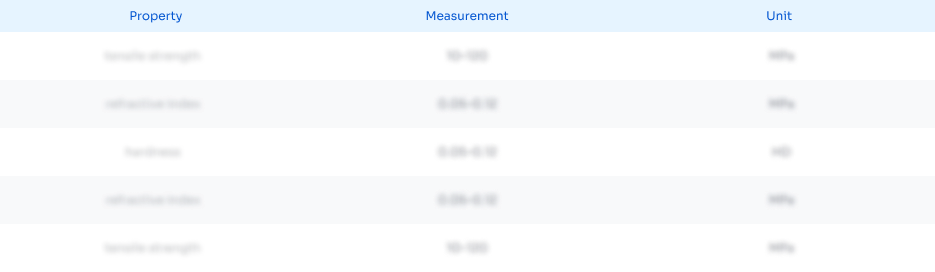
Abstract
Description
Claims
Application Information

- R&D
- Intellectual Property
- Life Sciences
- Materials
- Tech Scout
- Unparalleled Data Quality
- Higher Quality Content
- 60% Fewer Hallucinations
Browse by: Latest US Patents, China's latest patents, Technical Efficacy Thesaurus, Application Domain, Technology Topic, Popular Technical Reports.
© 2025 PatSnap. All rights reserved.Legal|Privacy policy|Modern Slavery Act Transparency Statement|Sitemap|About US| Contact US: help@patsnap.com