Cargo stacking robot
A technology for stacking robots and goods, which is applied to the stacking of objects, unstacking of objects, transportation and packaging, etc. It can solve the problems of complex stacking robot structure, poor stability of stacking robots, and low delivery accuracy. Achieve the effects of expansion, convenient stacking and neat goods, and wide application range
- Summary
- Abstract
- Description
- Claims
- Application Information
AI Technical Summary
Problems solved by technology
Method used
Image
Examples
Embodiment Construction
[0037] The specific implementation manners of the present invention will be further described in detail below in conjunction with the accompanying drawings and embodiments. The following examples are used to illustrate the present invention, but are not intended to limit the scope of the present invention.
[0038] refer to Figure 1 to Figure 8 , this embodiment provides a cargo stacking robot, including a base 1, a mechanical arm device 2 and a support device 3, the base 1 includes a first platform 11 and a second platform 12, the first platform 11 is equipped with a first translation The rotation device 4, the second platform 12 is equipped with a second translation rotation device 5, one end of the mechanical arm device 2 is rotatably connected to the first translation rotation device 4, one end of the support device 3 is rotatably connected to the second translation rotation device 5, and the mechanical arm The device 2 is connected with the supporting device 3;
[0039...
PUM
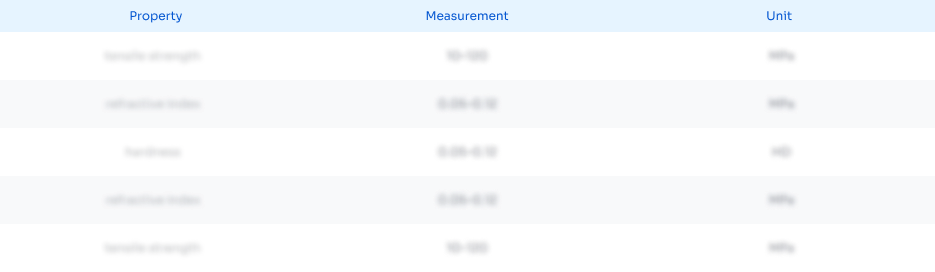
Abstract
Description
Claims
Application Information

- Generate Ideas
- Intellectual Property
- Life Sciences
- Materials
- Tech Scout
- Unparalleled Data Quality
- Higher Quality Content
- 60% Fewer Hallucinations
Browse by: Latest US Patents, China's latest patents, Technical Efficacy Thesaurus, Application Domain, Technology Topic, Popular Technical Reports.
© 2025 PatSnap. All rights reserved.Legal|Privacy policy|Modern Slavery Act Transparency Statement|Sitemap|About US| Contact US: help@patsnap.com