A General Pneumatic Muscle Embedded Controller
A technology of embedded controller and pneumatic muscle, which is applied in the field of integrated controller and high-frequency driver, which can solve the problems of low module precision, difficult selection of robot hardware, complicated wiring, etc.
- Summary
- Abstract
- Description
- Claims
- Application Information
AI Technical Summary
Problems solved by technology
Method used
Image
Examples
Embodiment Construction
[0027] The specific implementation manners of the present invention will be further described below in conjunction with the accompanying drawings and technical solutions.
[0028] figure 1 It is a schematic diagram of the layered structure of the pneumatic muscle embedded controller. The whole system includes: control layer, drive layer, and perception layer. Each layer has its own main circuit board. The three main circuit boards are stacked from bottom to top. The order is the control layer, the driving layer, and the sensing layer. Adjacent main circuit boards are connected by copper pillars.
[0029] figure 2It is a schematic diagram of the distribution of functional modules of the control layer, which mainly includes a power supply module, A / D and D / A conversion modules, PWM output modules, and counter modules. The power supply of the power module adopts +24V DC power supply, and the isolated DC-DC power converter HZD15D-24D15 of Huizhong Company is used to convert +24...
PUM
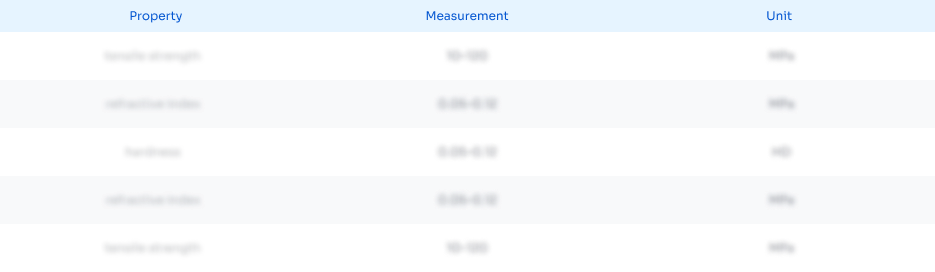
Abstract
Description
Claims
Application Information

- R&D
- Intellectual Property
- Life Sciences
- Materials
- Tech Scout
- Unparalleled Data Quality
- Higher Quality Content
- 60% Fewer Hallucinations
Browse by: Latest US Patents, China's latest patents, Technical Efficacy Thesaurus, Application Domain, Technology Topic, Popular Technical Reports.
© 2025 PatSnap. All rights reserved.Legal|Privacy policy|Modern Slavery Act Transparency Statement|Sitemap|About US| Contact US: help@patsnap.com