A method for theoretical calculation of quasi-static deformation of turning workpiece and actual measurement of dynamic deformation
A calculation method and quasi-static technology, applied to turning equipment, metal processing machinery parts, manufacturing tools, etc., can solve the problems that the turning force cannot be directly determined, cannot be measured by contact sensors, and cannot be sensed by displacement sensors, etc., to achieve Good long-term working performance, high sensitivity, and the effect of reducing quality problems
- Summary
- Abstract
- Description
- Claims
- Application Information
AI Technical Summary
Problems solved by technology
Method used
Image
Examples
Embodiment 1
[0113] Set the elastic modulus of the workpiece material E=2.0×10 5 MPa, shear yield strength τ=200MPa, shear angle φ=42°, friction angle β=-2°, tool rake angle γ=-5°, shaft radius r 0 =24mm, shaft length l=300mm, turning thickness b=1mm, turning width h=3mm, axial feed speed The turning force F=1.266kN is calculated according to the Merchant formula.
[0114] By theoretical calculation, image 3 The variation curves of the rotation angle θ at three given sections x=0.25l, x=0.5l, x=0.75l with the turning time are given when there is a thimble constraint. Figure 4 The variation curves of the workpiece rotation angle with the section position are given when t=25s, t=50s, t=75s. Figure 5 The deflection curves of three given sections x=0.25l, x=0.5l, x=0.75l with turning time are given when there is thimble constraint. Image 6 The variation curves of the workpiece deflection with the section position at t=25s, t=50s, t=75s are given when there is a thimble constraint. F...
PUM
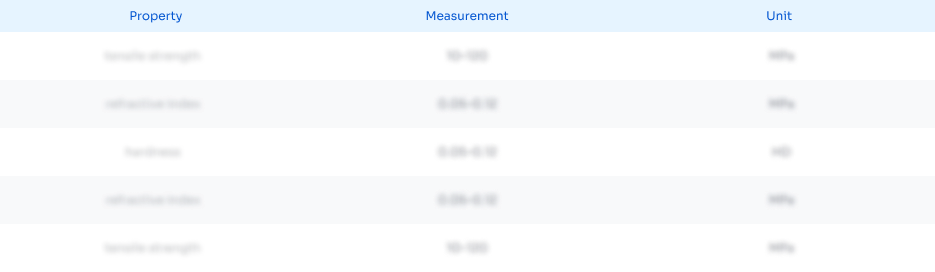
Abstract
Description
Claims
Application Information

- R&D
- Intellectual Property
- Life Sciences
- Materials
- Tech Scout
- Unparalleled Data Quality
- Higher Quality Content
- 60% Fewer Hallucinations
Browse by: Latest US Patents, China's latest patents, Technical Efficacy Thesaurus, Application Domain, Technology Topic, Popular Technical Reports.
© 2025 PatSnap. All rights reserved.Legal|Privacy policy|Modern Slavery Act Transparency Statement|Sitemap|About US| Contact US: help@patsnap.com