Machining system for downward core pulling casting piston
A processing system and piston technology, applied in metal processing equipment, casting molds, cores, etc., can solve the problems of guide rod clearance error, high product scrap rate, difficult temperature control, etc., to improve the positioning accuracy of the guide and improve the internal purity , Reduce the effect of shrinkage cavity shrinkage
- Summary
- Abstract
- Description
- Claims
- Application Information
AI Technical Summary
Problems solved by technology
Method used
Image
Examples
Embodiment
[0035] Such as Figures 1 to 9 As shown, a processing system for a lower core-pulling casting piston includes a blank processing device and a finishing device, the blank processing device includes a mold set for machining and forming a piston blank, and the mold set includes a metal outer mold 10, a metal top mold 20 and a metal inner mold 30, the lower end of the metal top mold 20 is embedded in the upper part of the metal outer mold 10, the upper end is higher than the upper plane of the metal outer mold 10, and the upper end of the metal inner mold 30 is embedded in the metal outer mold 10, and the lower end is lower than the lower plane of the metal outer mold 10, the forming cavity 50 of the piston is formed between the metal outer mold 10, the metal top mold 20 and the metal inner mold 30; the finishing device includes a fixing device, The pressing device, the guiding and positioning device and the processing knife 60 are fixedly installed on the fixing device, and the p...
PUM
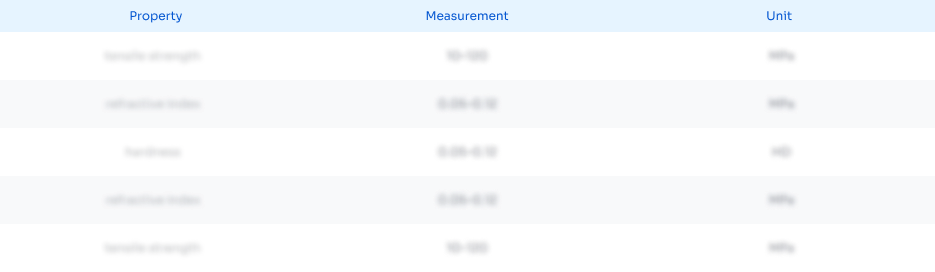
Abstract
Description
Claims
Application Information

- Generate Ideas
- Intellectual Property
- Life Sciences
- Materials
- Tech Scout
- Unparalleled Data Quality
- Higher Quality Content
- 60% Fewer Hallucinations
Browse by: Latest US Patents, China's latest patents, Technical Efficacy Thesaurus, Application Domain, Technology Topic, Popular Technical Reports.
© 2025 PatSnap. All rights reserved.Legal|Privacy policy|Modern Slavery Act Transparency Statement|Sitemap|About US| Contact US: help@patsnap.com