Single driving synchromesh corrugated-surface roller press
A synchronous meshing and corrugated surface technology, applied in the field of roller presses, can solve the problems of large line loss and reactive power loss, incomplete motor slip rate, increased roller surface wear, etc., and achieve line loss and reactive power loss. Low, reduce grinding energy consumption, avoid the effect of roller surface wear
- Summary
- Abstract
- Description
- Claims
- Application Information
AI Technical Summary
Problems solved by technology
Method used
Image
Examples
Embodiment Construction
[0036] Such as Figure 2-3 As shown, in one embodiment of the present invention, a single-drive synchronous meshing corrugated surface rolling machine 10 is disclosed for crushing materials. The single-drive synchronous meshing corrugated surface rolling machine 10 includes a main frame 1, two toothed Extrusion pair roller 2, double output synchronous reduction device 8 and motor 5, wherein:
[0037] The main frame 1 is a rectangular frame structure, which mainly provides rigid support for the two extrusion rollers 2. In the present invention, there is no special requirement for the structure selection of the main frame, just refer to the conventional selection in this field.
[0038] Two tooth-shaped extrusion rollers 2 are set on the main frame 1, and one of them is a corrugated fixed roller 22, and the other is a corrugated moving roller 23, please refer to Figure 2-4 As shown, the two corrugated rollers can ensure the stability of the toothed extrusion rollers during use...
PUM
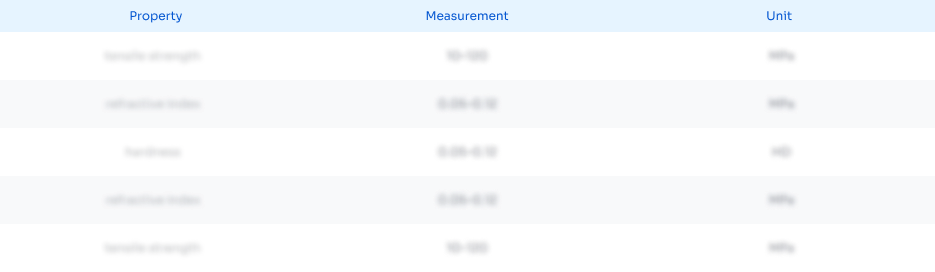
Abstract
Description
Claims
Application Information

- R&D Engineer
- R&D Manager
- IP Professional
- Industry Leading Data Capabilities
- Powerful AI technology
- Patent DNA Extraction
Browse by: Latest US Patents, China's latest patents, Technical Efficacy Thesaurus, Application Domain, Technology Topic, Popular Technical Reports.
© 2024 PatSnap. All rights reserved.Legal|Privacy policy|Modern Slavery Act Transparency Statement|Sitemap|About US| Contact US: help@patsnap.com