Manufacturing method of aluminum alloy cartridge shell and cartridge shell
A manufacturing method and technology of aluminum alloy, applied in the direction of cartridge ammunition, ammunition, anodizing, etc., can solve the problems of strength, deformation, high temperature resistance that cannot meet the requirements, difficult to achieve large plastic deformation, poor extrudability, etc. Achieving the effect of long finish retention time, excellent surface quality and fast cooling rate
- Summary
- Abstract
- Description
- Claims
- Application Information
AI Technical Summary
Problems solved by technology
Method used
Image
Examples
Embodiment 1
[0057] This embodiment provides a method for manufacturing an aluminum alloy shell, which specifically includes the following steps:
[0058] S1. Prepare aluminum alloy raw materials and melt aluminum alloy solution;
[0059] The aluminum alloy raw material in this embodiment is composed of the following alloy components in mass percentage: copper 4.0wt.%, magnesium 2.2wt.%, manganese 0.6wt.%, titanium 0.02wt.%, chromium 0.02wt.%, zirconium 0.01wt. .%, impurity iron, silicon content is 0.008wt.%, Al balance;
[0060] The preparation method of the above-mentioned aluminum alloy raw material is as follows: put aluminum with a purity of 99.99% into a melting furnace, heat it at 780°C until the aluminum is completely melted, then add copper, manganese, titanium, chromium, zirconium, and magnesium in sequence, melt for 45 minutes, and pass anhydrous nitrogen , refining for 25 minutes;
[0061] S2. Prepare the aluminum alloy shell blank: pour the aluminum alloy solution in step S1...
Embodiment 2
[0080] This embodiment provides a method for manufacturing an aluminum alloy shell, referring to the operation steps of Embodiment 1, the difference is that in step S1, the aluminum alloy raw material is composed of the following alloy components in mass percentages: copper 3.0wt.%, magnesium 3.0wt.% , manganese 1.0wt.%, titanium 0.03wt.%, chromium 0.03wt.%, zirconium 0.03wt.%, impurity iron, silicon content is 0.01wt.%, and the balance is Al element; In step S2, atomization injection pressure is 2.5MPa; in step S3, the stamping speed is 60mm / min, and the mixing ratio of graphite powder and cylinder oil is 3:5; in step S4, the anodic oxidation process parameters are: voltage 30V, current density 2.5A / dm 2 , anodizing temperature is 0 ℃, time is 2h.
Embodiment 3
[0082] This embodiment provides a method for manufacturing an aluminum alloy shell, referring to the operation steps of Embodiment 1, the difference is that in step S1, the aluminum alloy raw material is composed of the following alloy components in mass percentages: copper 5.0wt.%, magnesium 2.0wt.% , manganese 0.5wt.%, titanium 0.01wt.%, chromium 0.01wt.%, zirconium 0.03wt.%, impurity iron, silicon content are 0.009wt.%, and the balance is Al element; In step S2, the atomization injection pressure is 0.5MPa; in step S3, the stamping speed is 1mm / min, and the mixing ratio of graphite powder and cylinder oil is 5:7; in step S4, the anodic oxidation process parameters are: voltage 5V, current density 2A / dm 2 , the anodizing temperature is 5°C, and the time is 2h.
PUM
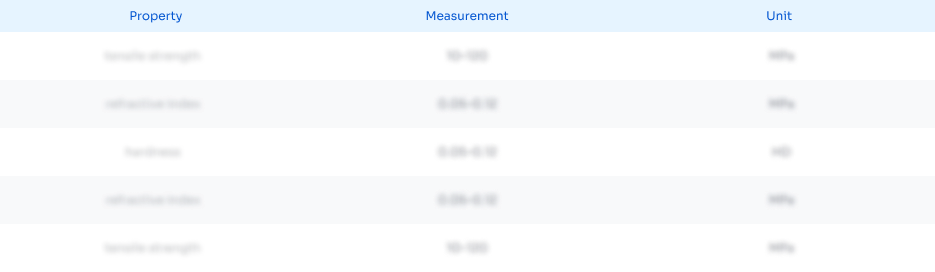
Abstract
Description
Claims
Application Information

- R&D
- Intellectual Property
- Life Sciences
- Materials
- Tech Scout
- Unparalleled Data Quality
- Higher Quality Content
- 60% Fewer Hallucinations
Browse by: Latest US Patents, China's latest patents, Technical Efficacy Thesaurus, Application Domain, Technology Topic, Popular Technical Reports.
© 2025 PatSnap. All rights reserved.Legal|Privacy policy|Modern Slavery Act Transparency Statement|Sitemap|About US| Contact US: help@patsnap.com