Concrete filled steel tubular column construction method
A technology of steel pipe concrete columns and construction methods, applied in the direction of columns, pier columns, pillars, etc., can solve problems such as difficulty in ensuring compactness and strength, and achieve the effect of improving compactness and strength
- Summary
- Abstract
- Description
- Claims
- Application Information
AI Technical Summary
Problems solved by technology
Method used
Image
Examples
Embodiment Construction
[0024] It includes the following steps:
[0025] Step 1. Prepare self-compacting concrete and install steel pipe columns;
[0026] When preparing self-compacting concrete, its components are proportioned according to parts by weight, and the slump of the concrete after the proportioning is completed ranges from 550mm to 655mm. The installation of the steel pipe column is carried out simultaneously with the preparation of self-compacting concrete. The specific installation method of the steel pipe column is not particularly limited in this embodiment, and the installation method can adopt the existing installation method.
[0027] Step 2: Pouring the prepared self-compacting concrete from the top of the steel pipe column, using a high-frequency vibrating rod with a length of at least nine meters for auxiliary vibration during pouring, and auxiliary vibration for every two-meter-thick concrete layer.
[0028] During the auxiliary vibration in this step, the high-frequency vib...
PUM
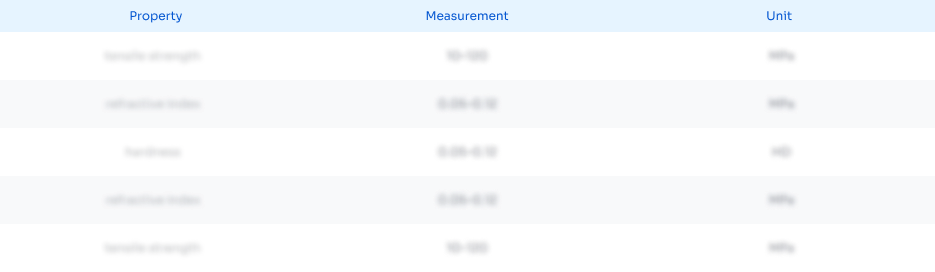
Abstract
Description
Claims
Application Information

- R&D Engineer
- R&D Manager
- IP Professional
- Industry Leading Data Capabilities
- Powerful AI technology
- Patent DNA Extraction
Browse by: Latest US Patents, China's latest patents, Technical Efficacy Thesaurus, Application Domain, Technology Topic, Popular Technical Reports.
© 2024 PatSnap. All rights reserved.Legal|Privacy policy|Modern Slavery Act Transparency Statement|Sitemap|About US| Contact US: help@patsnap.com