Steel base surface alloying-ion nitriding wear-resistant corrosion-resistant composite modified layer and preparation method thereof
A technology of surface alloying and ion nitriding, applied in metal material coating process, coating, solid-state diffusion coating, etc., can solve slow nitriding speed, brittle peeling of nitriding layer, wear resistance and corrosion resistance Low-level problems, to achieve the effect of improving the hardness gradient, strengthening the strength support, and enhancing the ability to resist fatigue and wear
- Summary
- Abstract
- Description
- Claims
- Application Information
AI Technical Summary
Problems solved by technology
Method used
Image
Examples
Embodiment 1
[0048] A method for preparing a steel base surface alloying-ion nitriding wear-resistant and corrosion-resistant composite modified layer, the alloy modified layer formula is as follows: calculated in parts by weight:
[0049] Cr 64.5 parts, Ni 32.3 parts, Ti 1.6 parts, La 1.6 parts;
[0050] The specific steps are as follows:
[0051] (1) Preparation of alloy target
[0052] Precisely weigh Cr, Ni, Ti and La metal powders with a purity of more than 99.9% according to the above formula, mix them, and pour them into a φ40mm mold after fully stirring, pressurize to 30MPa with a powder tablet press to form a diameter of φ40mm , a wafer sample with a thickness of 3 mm is put into a vacuum sintering furnace and sintered into a source target;
[0053] (2) Double-layer glow metal infiltration process
[0054] In the vacuum container of the ion nitriding equipment, the low and medium carbon steel workpieces are placed on the cathode seat, the source target is placed between the ano...
Embodiment 2
[0065] A method for preparing a steel base surface alloying-ion nitriding wear-resistant and corrosion-resistant composite modified layer, the alloy modified layer formula is as follows: calculated in parts by weight:
[0066] 64.7 parts of Cr, 32.5 parts of Ni, 1.6 parts of Ti, 1.2 parts of La;
[0067] The specific steps are as follows:
[0068] (1) Preparation of alloy target
[0069] Precisely weigh Cr, Ni, Ti and La metal powders with a purity of more than 99.9% according to the above formula, mix them, and pour them into a φ40mm mold after fully stirring, pressurize to 30MPa with a powder tablet press to form a diameter of φ40mm , a wafer sample with a thickness of 3 mm is put into a vacuum sintering furnace and sintered into a source target;
[0070] (2) Double-layer glow metal infiltration process
[0071] In the vacuum container of the ion nitriding equipment, place the low and medium carbon steel workpiece on the cathode seat, place the source target between the a...
Embodiment 3
[0082] A method for preparing a steel base surface alloying-ion nitriding wear-resistant and corrosion-resistant composite modified layer, the alloy modified layer formula is as follows: calculated in parts by weight:
[0083] 64.2 parts of Cr, 32.2 parts of Ni, 2.0 parts of Ti, 1.6 parts of La;
[0084] For the specific steps, refer to the parameters in Examples 1 and 2. The steel base surface alloying-ion nitriding wear-resistant and corrosion-resistant composite modified layer prepared in this example has the following effects:
[0085] 1. The hardness of the prepared alloy layer is about 3.5 times that of the matrix. Compared with Example 1, due to the increase of Ti content, excessive TiN phase is generated in the alloy layer, the hardness increases, and the brittleness increases;
[0086]2. After alloying, the ion nitriding speed and the thickness of the nitrided layer are about 4 times that of conventional ion nitriding. Compared with Example 1, due to the same rare e...
PUM
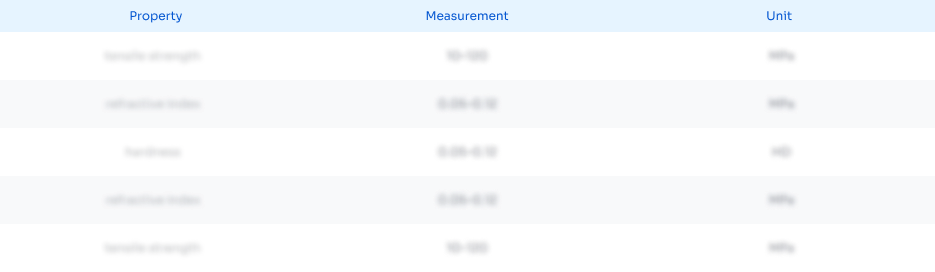
Abstract
Description
Claims
Application Information

- Generate Ideas
- Intellectual Property
- Life Sciences
- Materials
- Tech Scout
- Unparalleled Data Quality
- Higher Quality Content
- 60% Fewer Hallucinations
Browse by: Latest US Patents, China's latest patents, Technical Efficacy Thesaurus, Application Domain, Technology Topic, Popular Technical Reports.
© 2025 PatSnap. All rights reserved.Legal|Privacy policy|Modern Slavery Act Transparency Statement|Sitemap|About US| Contact US: help@patsnap.com