Technology for processing vanadium extraction semi-steel
A processing technology and a vanadium slag technology, applied in the field of vanadium extraction semi-steel processing technology, can solve the problems of increasing production and maintenance costs of enterprises, increasing the difficulty of maintaining furnace conditions, and decreasing the operation rate of converters, so as to improve the operation rate of converters and reduce the consumption of lime. , the effect is improved
- Summary
- Abstract
- Description
- Claims
- Application Information
AI Technical Summary
Problems solved by technology
Method used
Image
Examples
Embodiment 1
[0027] In an embodiment of the present invention, a vanadium extraction semi-steel processing technology includes the following process flow:
[0028] (1) Feed pig iron; (2) Add iron; (3) blowing; (4) add coolant; (5) end blowing;
[0029] Further, the following steps are included:
[0030] (1) Import pig iron: carry out desulfurization and slag removal of pig iron, and the work of removing slag from molten iron needs to be strengthened. The slag removal rate of molten iron in the mixed iron furnace is 100%. It is strictly forbidden to bring sediment into the pig iron into the furnace. After desulfurization and slag removal, molten pig iron is obtained;
[0031] (2) Add iron: mix the obtained molten pig iron into the converter, the charging amount is based on molten iron: 29.2 tons, pig iron: 1.09 tons, and the temperature of the molten iron into the furnace is set at 1225 degrees, in order to facilitate the control of the temperature process of the converter to extract vanadi...
Embodiment 2
[0045] In an embodiment of the present invention, a vanadium extraction semi-steel processing technology includes the following process flow:
[0046] (2) Feed pig iron; (2) Mix iron; (3) blowing; (4) add coolant; (5) end blowing;
[0047] Further, the following steps are included:
[0048] (1) Import pig iron: carry out desulfurization and slag removal of pig iron, and the work of removing slag from molten iron needs to be strengthened. The slag removal rate of molten iron in the mixed iron furnace is 100%. It is strictly forbidden to bring sediment into the pig iron into the furnace. After desulfurization and slag removal, molten pig iron is obtained;
[0049] (2) Add iron: mix the obtained molten pig iron into the converter, the charging amount is based on molten iron: 29.8 tons, pig iron: 1.47 tons, and the temperature of molten iron entering the furnace is set at 1245 degrees to facilitate the process control of the temperature process of vanadium extraction in the conver...
Embodiment 4
[0080] In an embodiment of the present invention, a vanadium extraction semi-steel processing technology includes the following process flow:
[0081] (4) Feed pig iron; (2) Mix iron; (3) blowing; (4) add coolant; (5) end blowing;
[0082] Further, the following steps are included:
[0083] (1) Import pig iron: carry out desulfurization and slag removal of pig iron, and the work of removing slag from molten iron needs to be strengthened. The slag removal rate of molten iron in the mixed iron furnace is 100%. It is strictly forbidden to bring sediment into the pig iron into the furnace. After desulfurization and slag removal, molten pig iron is obtained;
[0084] (2) Add iron: mix the obtained molten pig iron into the converter, the loading amount is based on molten iron: 29.3 tons, pig iron: 1.37 tons, and the temperature of the molten iron into the furnace is set at 1240 degrees, in order to facilitate the control of the temperature process of the converter to extract vanadiu...
PUM
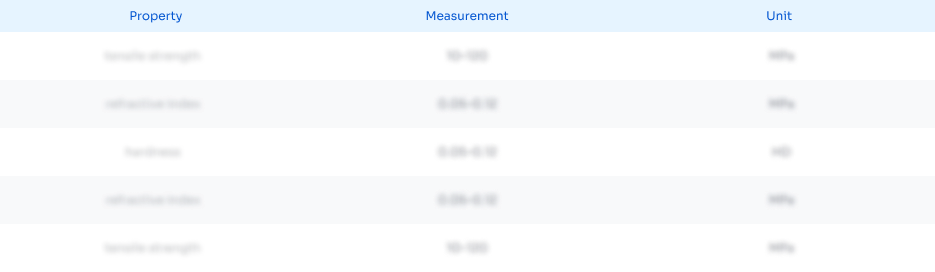
Abstract
Description
Claims
Application Information

- R&D
- Intellectual Property
- Life Sciences
- Materials
- Tech Scout
- Unparalleled Data Quality
- Higher Quality Content
- 60% Fewer Hallucinations
Browse by: Latest US Patents, China's latest patents, Technical Efficacy Thesaurus, Application Domain, Technology Topic, Popular Technical Reports.
© 2025 PatSnap. All rights reserved.Legal|Privacy policy|Modern Slavery Act Transparency Statement|Sitemap|About US| Contact US: help@patsnap.com