Equipment and process of utilizing MVR technology to recover waste heat
A waste heat recovery and waste heat technology, applied in the chemical industry, sustainable manufacturing/processing, climate sustainability, etc., to achieve the effects of simple process flow, low operating cost, and good economic benefits
- Summary
- Abstract
- Description
- Claims
- Application Information
AI Technical Summary
Problems solved by technology
Method used
Image
Examples
Embodiment 1
[0027] This embodiment provides a device for recovering waste heat using MVR technology, which is used to recover waste heat in the rectification process of epichlorohydrin, recover and treat the waste heat steam at the top of the rectification tower, and reuse it as a new heat source for purification in the rectification system of heating steam.
[0028] Please refer to figure 1 , the equipment for recovering waste heat using MVR technology includes a falling film heat exchanger 1, a falling film separator 2, and a secondary separator 3 connected in sequence through pipelines, and the falling film heat exchanger 1 is also connected with a phase separation Device 4, the phase separation device 4 is a phase separation tank, the secondary separator 3 is connected with a compressor 5 and a liquid accumulation device 6 through pipelines, and the liquid accumulation device 6 is a liquid accumulation storage tank.
[0029] Further, the falling film heat exchanger 1 is connected wit...
Embodiment 2
[0033] This embodiment provides a process for recovering waste heat using the equipment described in Example 1, the process is used to treat the mixed steam of epichlorohydrin and water with a flow rate of 15.25t / h, wherein the flow rate of epichlorohydrin is 6.25t / h The flow rate of t / h, water is 9t / h, and described technique comprises the steps:
[0034] S1. Recover the waste heat of the mixed steam of epichlorohydrin and water at the top of the rectification tower, and use the mixed steam of epichlorohydrin and water after rectification as a heat source to enter the falling film heat exchanger 1 through the pipeline for heat exchange, specifically Ground, the mixed steam enters the shell side of the falling film heat exchanger 1, and exchanges heat with the water in the tube side of the falling film heat exchanger 1, and the mixed steam of epichlorohydrin and water is condensed into epichlorohydrin and water after heat exchange The mixed liquid, the mixed liquid flows throu...
experiment example
[0039] The waste heat recovery process described in Example 2 was tested for the operation energy consumption in the process of rectifying epichlorohydrin, and the results are shown in Table 1.
[0040] Table 1
[0041]
[0042] The above results show that the waste heat recovery equipment and process using MVR technology described in Example 2 has the advantages of low energy consumption and cost, high output, simple process, less equipment, less construction investment, etc., and can reduce the annual cost by 10,437,084 Yuan.
PUM
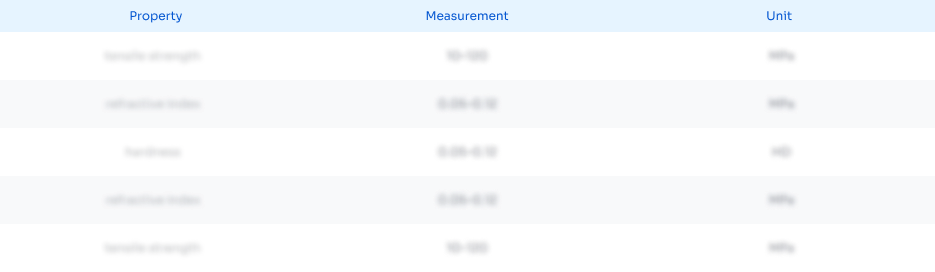
Abstract
Description
Claims
Application Information

- R&D Engineer
- R&D Manager
- IP Professional
- Industry Leading Data Capabilities
- Powerful AI technology
- Patent DNA Extraction
Browse by: Latest US Patents, China's latest patents, Technical Efficacy Thesaurus, Application Domain, Technology Topic, Popular Technical Reports.
© 2024 PatSnap. All rights reserved.Legal|Privacy policy|Modern Slavery Act Transparency Statement|Sitemap|About US| Contact US: help@patsnap.com