Sludge solidifying agent prepared from slag and its preparation method and application
A curing agent and sludge technology, applied in the field of sludge curing agent and its preparation, can solve the problems of long curing time, endangering the ecological environment, poor durability, etc.
- Summary
- Abstract
- Description
- Claims
- Application Information
AI Technical Summary
Problems solved by technology
Method used
Image
Examples
Embodiment 1
[0035] A kind of sludge curing agent prepared by using slag provided in Example 1 is prepared by the following method: first prepare raw materials according to the following mass percentages: 25% slag, 20% modified diatomite, 22% attapulgite , 10% microsilica, 4% powdered activated carbon, 5% potassium peroxide, 2% potassium permanganate, 1.5% iron powder, 3.5% cationic chelate, 3% polyrotaxane, 3% sodium polyacrylate, 0.5 % calcium hydroxide, 0.3% naphthalene-based superplasticizer, 0.2% polyacrylamide, fully mix and stir the above raw materials in a mixer; the cationic chelate is made of ethylenediaminetetraacetic acid (EDTA) and iron ion chelate combined.
[0036] The above sludge curing agent is mixed into the sludge according to the ratio of the mass ratio of the sludge to 25%, and then fully mixed, and then naturally aired and solidified for 0.8 hours to obtain the solidified sludge.
Embodiment 2
[0037] A kind of sludge curing agent prepared by using slag provided in Example 2 is prepared by the following method: first prepare raw materials according to the following mass percentages: 20% slag, 23% modified diatomite, 21% attapulgite , 14% microsilica, 6% powdered activated carbon, 6% magnesium peroxide, 1% potassium permanganate, 1% iron powder, 2% cationic chelate, 3% polyrotaxane, 2.4% sodium polyacrylate, 0.3 % sodium silicate, 0.2% naphthalene-based superplasticizer, 0.1% polyacrylamide, fully mix and stir the above raw materials in a mixer; the cationic chelate is composed of ethylenediaminetetraacetic acid (EDTA) and calcium ion chelate combined.
[0038]The sludge solidifying agent and the sludge in Example 2 were added into the sludge according to the mixing ratio of 15% by mass, and then fully mixed, and allowed to dry naturally for 1 hour before use.
Embodiment 3
[0039] A kind of sludge curing agent prepared by using slag provided in Example 3 is prepared by the following method: first prepare raw materials according to the following mass percentages: 15% slag, 24% modified diatomite, 20% attapulgite , 15% microsilica, 8% powdered activated carbon, 5% calcium peroxide, 2% potassium permanganate, 2.2% iron powder, 4% cationic chelate, 1.5% polyrotaxane, 2% sodium polyacrylate, 0.6 % calcium hydroxide, 0.4% naphthalene-based superplasticizer, 0.3% polyaluminum chloride, fully mix and stir the above raw materials in a mixer; the cationic chelate is composed of dihydroxyethylglycine (DEG) and magnesium ions Chelated.
[0040] The sludge solidifying agent and the sludge in Example 1 were added into the sludge according to the mixing ratio of 25% by mass, and then fully mixed, and allowed to dry naturally for 0.7 hours before use.
PUM
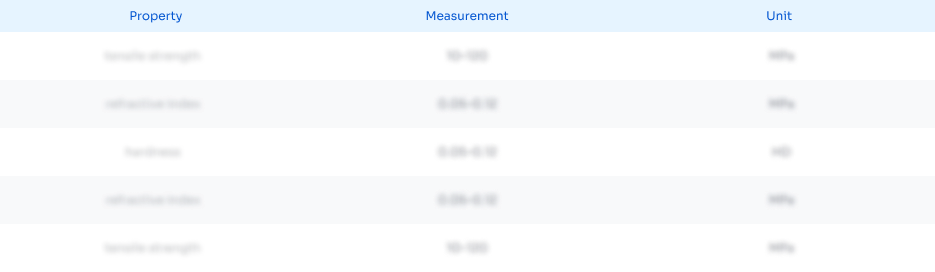
Abstract
Description
Claims
Application Information

- R&D
- Intellectual Property
- Life Sciences
- Materials
- Tech Scout
- Unparalleled Data Quality
- Higher Quality Content
- 60% Fewer Hallucinations
Browse by: Latest US Patents, China's latest patents, Technical Efficacy Thesaurus, Application Domain, Technology Topic, Popular Technical Reports.
© 2025 PatSnap. All rights reserved.Legal|Privacy policy|Modern Slavery Act Transparency Statement|Sitemap|About US| Contact US: help@patsnap.com