Production process of manganese sulfate
A production process and technology of manganese sulfate, applied in the preparation of manganese sulfate and manganese compounds, etc., can solve problems such as pollution of the environment, and achieve the effect of reducing pollution and ensuring quality
- Summary
- Abstract
- Description
- Claims
- Application Information
AI Technical Summary
Problems solved by technology
Method used
Image
Examples
Embodiment 1
[0034] 1) Use a loaded organic extractant composed of Lix973 extractant with a volume ratio of 5% mixed with 260# solvent oil to treat the by-products after cobalt smelting (the by-products after cobalt smelting include: manganese 80g / L, copper 10g / L, Zinc 2g / l calcium 8g / L, surplus is metal or non-metal impurity) extracts, and collects raffinate, makes the first intermediate mixed solution after removing copper; 2) adds sodium hypochlorite in above-mentioned first intermediate mixed solution, Stirring and reacting for 4 hours, standing and aging for 1 day, separating and precipitating to obtain the second intermediate mixed solution after decalcification; The two intermediate mixtures are extracted, the oil phase is collected, and an organic phase loaded with manganese is obtained; 4) sulfuric acid is used to back-extract the organic phase loaded with manganese, and the aqueous phase is collected to obtain a manganese sulfate solution; 5) the above manganese sulfate is prepare...
Embodiment 2
[0036] 1) Use a loaded organic extractant composed of Lix973 extractant with a volume ratio of 10% mixed with 260# solvent oil to treat by-products after cobalt smelting (by-products after cobalt smelting include: manganese 70g / L, copper 11gL, zinc 2g / L, calcium 10g / L, the rest is metal or non-metallic impurity) to extract, collect raffinate, make the first intermediate mixed solution after copper removal; 2) add sodium hypochlorite in above-mentioned first intermediate mixed solution, stir After reacting for 5 hours, standing and aging for 2 days, separating and precipitating to obtain the second intermediate mixed solution after decalcification; The intermediate mixed solution is extracted, and the oil phase is collected to obtain an organic phase loaded with manganese; 4) back-extracting the organic phase loaded with manganese with sulfuric acid, and the aqueous phase is collected to obtain a manganese sulfate solution; 5) the above manganese sulfate solution is Perform ev...
Embodiment 3
[0038] 1) Use a loaded organic extractant composed of Lix973 extractant with a volume ratio of 15% mixed with 260# solvent oil to treat the by-products after cobalt smelting (the by-products after cobalt smelting include: manganese 50g / L, copper 5g / L, Zinc 1g / L, calcium 6g / L, and the remainder is metal or non-metallic impurities) to extract, collect the raffinate, and obtain the first intermediate mixed solution after copper removal; 2) add sodium hypochlorite to the above-mentioned first intermediate mixed solution , stirred and reacted for 6h, after standing and aging for 3d, separated and precipitated to obtain the second intermediate mixed solution after decalcification; The second intermediate mixture is extracted, the oil phase is collected, and an organic phase loaded with manganese is obtained; 4) sulfuric acid is used to back-extract the organic phase loaded with manganese, and the aqueous phase is collected to obtain a manganese sulfate solution; 5) the above-mentione...
PUM
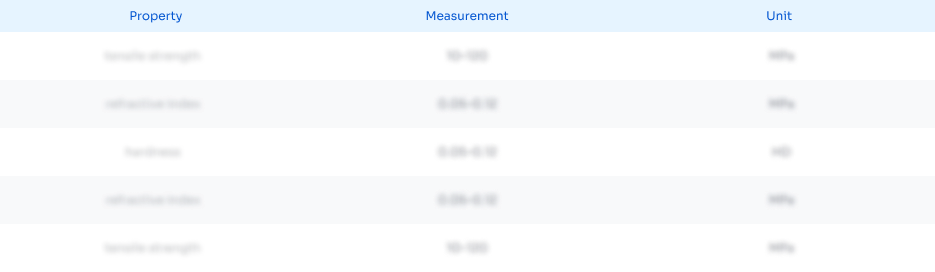
Abstract
Description
Claims
Application Information

- R&D
- Intellectual Property
- Life Sciences
- Materials
- Tech Scout
- Unparalleled Data Quality
- Higher Quality Content
- 60% Fewer Hallucinations
Browse by: Latest US Patents, China's latest patents, Technical Efficacy Thesaurus, Application Domain, Technology Topic, Popular Technical Reports.
© 2025 PatSnap. All rights reserved.Legal|Privacy policy|Modern Slavery Act Transparency Statement|Sitemap|About US| Contact US: help@patsnap.com