Two-degree-of-freedom internal model control analysis method for industrial heating furnace
A technology of control analysis and degree of freedom, applied in the field of automation, can solve problems such as insufficient control accuracy
- Summary
- Abstract
- Description
- Claims
- Application Information
AI Technical Summary
Problems solved by technology
Method used
Image
Examples
Embodiment Construction
[0069]The present invention will be further described below.
[0070] Take the actual industrial heating furnace temperature control as an example:
[0071] Step 1, establish the process model of the heating furnace, the specific steps are:
[0072] 1.1 First consider the input and output temperature data of the heating process of the industrial heating furnace, and establish the model transfer function of the heating furnace and the standard proportional-integral-derivative controller transfer function, as shown in the following formula:
[0073]
[0074]
[0075] Among them, P(s) is the model of the heating process of the heating furnace, K is the process gain coefficient; T is the process time constant; τ represents the delay time; C(s) is the transfer function of the PID controller; K c is the proportional gain of the controller; T i is the integral time constant of the controller; T d is the derivative time constant of the controller.
[0076] 1.2 Suppose there ...
PUM
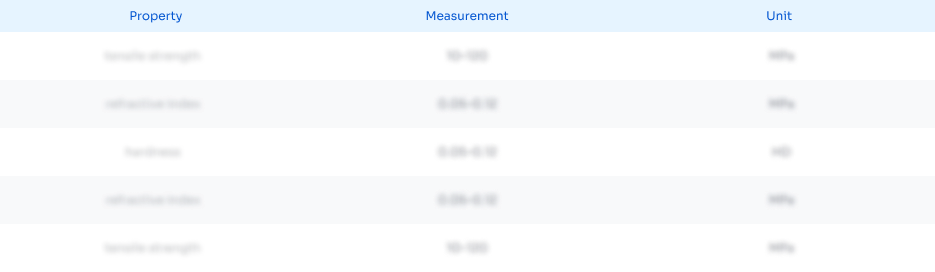
Abstract
Description
Claims
Application Information

- R&D Engineer
- R&D Manager
- IP Professional
- Industry Leading Data Capabilities
- Powerful AI technology
- Patent DNA Extraction
Browse by: Latest US Patents, China's latest patents, Technical Efficacy Thesaurus, Application Domain, Technology Topic, Popular Technical Reports.
© 2024 PatSnap. All rights reserved.Legal|Privacy policy|Modern Slavery Act Transparency Statement|Sitemap|About US| Contact US: help@patsnap.com