Preparation method and system for bamboo fiber rope
A preparation system, bamboo fiber technology, applied in rope-making auxiliary devices, manufacturing tools, mechanical equipment, etc., can solve the problems of low content of bamboo fiber, destruction of bamboo natural characteristics, and inability to maximize the excellent performance of bamboo fiber, etc., to achieve Strong water absorption, improved industrial production efficiency, and good rigidity
- Summary
- Abstract
- Description
- Claims
- Application Information
AI Technical Summary
Problems solved by technology
Method used
Image
Examples
preparation example Construction
[0050] see Figure 1-3 Shown, the present invention relates to a kind of preparation method of bamboo fiber rope, described method concrete steps are as follows:
[0051] Step (1) Whole bamboo treatment: select 1-2 year-old fresh tender bamboo, remove branches, and clean the outer surface of bamboo; bamboo here includes economical bamboos such as moso bamboo, Ci bamboo, yellow bamboo, green bamboo;
[0052] Step (2) sawing the bamboo tube: after the bamboo is cleaned, use a circular saw 1 to cut it into sections, and the length of the bamboo section is sawed into 1-3m according to different specifications;
[0053] Step (3) colliding table fragmentation: Utilize the colliding table bamboo cutting machine 2 to carry out the fragmentation process of the bamboo section, and the bamboo section is divided into 12-32 parts according to different specifications in the direction of the bamboo tube cross section, and made into 1-2cm wide bamboo chips ;
[0054] Step (4) splitting the...
Embodiment 1
[0071] Step (1) Whole bamboo treatment: select 1-year-old fresh tender bamboo, remove the branches, and clean the outer surface of the bamboo; the bamboo here includes economical bamboos such as Moso bamboo, Ci bamboo, yellow bamboo, and green bamboo;
[0072] Step (2) sawing the bamboo tube: after the bamboo is cleaned, use a circular saw 1 to cut it into sections, and the length of the bamboo section is sawed into 1m according to different specifications;
[0073] Step (3) colliding table fragmentation: Utilize the colliding table bamboo cutting machine 2 to carry out the fragmentation process of the bamboo section, and the bamboo section is divided into 16 parts according to different specifications in the direction of the cross-section of the bamboo tube, and made into 2cm wide bamboo chips;
[0074] Step (4) splitting the bamboo strips: using the bamboo strip splitter 3 to divide the bamboo strips into 5 layers according to different thicknesses to obtain 2mm thick bamboo ...
Embodiment 2
[0084] Step (1) Whole bamboo treatment: select 1.5-year-old fresh and tender bamboo, remove the branches, and clean the outer surface of the bamboo; the bamboo here includes economical bamboos such as Moso bamboo, Ci bamboo, yellow bamboo, and green bamboo;
[0085] Step (2) sawing the bamboo tube: after the bamboo is cleaned, use a circular saw 1 to cut it into sections, and the length of the bamboo section is sawed into 2m according to different specifications;
[0086] Step (3) colliding table fragmentation: Utilize the colliding table bamboo cutting machine 2 to carry out the fragmentation process of the bamboo section, and the bamboo section is divided into 25 parts according to different specifications in the direction of the cross-section of the bamboo tube, and made into 1.5cm wide bamboo chips;
[0087] Step (4) splitting the bamboo strips: using the bamboo strip splitter 3 to divide the bamboo strips into 6 layers according to different thicknesses to obtain 1mm thick...
PUM
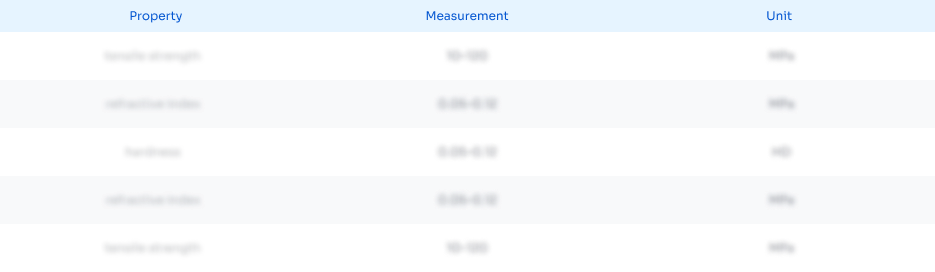
Abstract
Description
Claims
Application Information

- R&D
- Intellectual Property
- Life Sciences
- Materials
- Tech Scout
- Unparalleled Data Quality
- Higher Quality Content
- 60% Fewer Hallucinations
Browse by: Latest US Patents, China's latest patents, Technical Efficacy Thesaurus, Application Domain, Technology Topic, Popular Technical Reports.
© 2025 PatSnap. All rights reserved.Legal|Privacy policy|Modern Slavery Act Transparency Statement|Sitemap|About US| Contact US: help@patsnap.com