A method for reduce that residual alkali on the surface of high nickel material
A processing method, high-nickel technology, applied in nanotechnology for materials and surface science, electrical components, electrochemical generators, etc., can solve the problems of coating, high-nickel material rate and cycle performance decline, increase battery irreversibility capacity loss and other issues, to achieve the effect of reducing residual alkali, improving processing performance and electrochemical performance
- Summary
- Abstract
- Description
- Claims
- Application Information
AI Technical Summary
Problems solved by technology
Method used
Image
Examples
Embodiment 1
[0027] The high-nickel material used in this embodiment is LiNi 0.85 co 0.1 mn 0.05 o 2 , the surface residual alkali treatment steps are as follows:
[0028] (1) Cleaning: the high nickel material LiNi 0.85 co 0.1 mn 0.05 o 2 placed in supercritical CO 2 In the extraction kettle, at room temperature, under the condition of 10MPa, clean for 0.2 hours, repeat the above cleaning process 3 times;
[0029] (2) Coating: inject Al into the sub-pump of the extraction kettle 2 o 3 aqueous solution with supercritical CO 2 Carry out coating treatment, under the conditions of room temperature and 10MPa, treat for 0.2 hours, wherein Al 2 o 3 The amount of high nickel material LiNi 0.85 co 0.1 mn 0.05 o 2 0.2% of the mass percentage, repeat the above coating process 2 times;
[0030] (3) Sintering: Heat the treated powder to 600°C in an oxygen atmosphere, keep it warm for 5 hours, and then cool it naturally to obtain LiNi, a high-nickel material with low residual alkali 0...
Embodiment 2
[0032] The high-nickel material used in this embodiment is LiNi 0.6 co 0.2 mn 0.2 o 2 , the surface residual alkali treatment steps are as follows:
[0033] (1) Cleaning: the high nickel material LiNi 0.6 co 0.2 mn 0.2 o 2 Place in an extraction kettle equipped with supercritical methanol, wash for 0.1 hour at room temperature and 20MPa, and repeat the above cleaning process twice;
[0034] (2) Coating: Add Al 2 o 3 , ZrO 2 and TiO 2 ethanol solution with supercritical CO 2 Carry out cladding treatment, under the conditions of room temperature and 20MPa, treat for 0.1 hour, wherein Al 2 o 3 , ZrO 2 and TiO 2 The amount of high nickel material LiNi 0.6 co 0.2 mn 0.2 o 2 0.4% of the mass percentage, coated once;
[0035](3) Sintering: Heat the treated powder to 300°C in an oxygen atmosphere, keep it warm for 5 hours, and then cool it naturally to obtain LiNi, a high-nickel material with low residual alkali 0.6 co 0.2 mn 0.2 o 2 .
Embodiment 3
[0037] The high-nickel material used in this embodiment is LiNiO 2 , the surface residual alkali treatment steps are as follows:
[0038] (1) Cleaning: the high nickel material LiNiO 2 placed in supercritical CO 2 In the extraction kettle, at room temperature and under the condition of 35MPa, wash for 0.5 hour and wash once;
[0039] (2) Coating: inject Al(OH) into the auxiliary pump of the extraction kettle 3 aqueous solution with supercritical CO 2 Carry out coating treatment, under the conditions of room temperature and 35MPa, treat for 0.5 hours, wherein Al(OH) 3 The amount of high nickel material LiNiO 2 0.3% of the mass percentage, coated once;
[0040] (3) Sintering: Heat the treated powder to 800°C in compressed dry air, keep it warm for 5 hours, and then cool it naturally to obtain LiNiO, a high-nickel material with low residual alkali 2 .
PUM
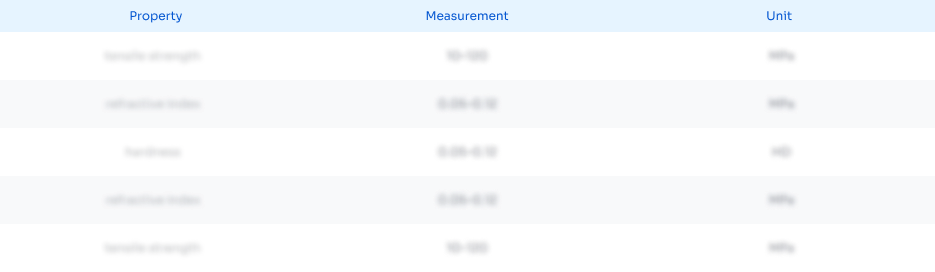
Abstract
Description
Claims
Application Information

- R&D
- Intellectual Property
- Life Sciences
- Materials
- Tech Scout
- Unparalleled Data Quality
- Higher Quality Content
- 60% Fewer Hallucinations
Browse by: Latest US Patents, China's latest patents, Technical Efficacy Thesaurus, Application Domain, Technology Topic, Popular Technical Reports.
© 2025 PatSnap. All rights reserved.Legal|Privacy policy|Modern Slavery Act Transparency Statement|Sitemap|About US| Contact US: help@patsnap.com