High-temperature-resistant winding and manufacturing method thereof, motor and electric appliance
A production method and high temperature resistant technology, which is applied in the manufacture of motor generators, the shape/style/structure of winding conductors, electrical components, etc., can solve the problems of poor temperature resistance of motors and difficulty reaching above 300°C, and achieve high temperature resistance The effect of high temperature
- Summary
- Abstract
- Description
- Claims
- Application Information
AI Technical Summary
Problems solved by technology
Method used
Image
Examples
Embodiment 1
[0044] See figure 1 Now, the manufacturing method of the high temperature resistant winding provided by the present invention will be described. The manufacturing method of the high temperature resistant winding includes the following steps:
[0045] S1 adopts a high-temperature resistant wire to be wound into a coil, the wire includes a conductor made of conductive metal and an insulating surface layer made of inorganic insulating material, the insulating surface layer is wrapped on the conductor;
[0046] S2 set a mold, and place the wound coil in the mold;
[0047] S3 provides high-temperature-resistant inorganic insulating materials and makes them into slurry;
[0048] S4 pour the slurry into the mold, and solidify the slurry and the coil into an integrated structure;
[0049] S5 opens the mold to obtain a high temperature resistant winding.
[0050] The present invention adopts a high temperature resistant wire to make a coil, and the insulating surface layer of the coil is made of...
specific Embodiment approach
[0053] Further, see figure 1 As a specific implementation of the method for manufacturing a high temperature resistant winding provided by the present invention, the manufacturing steps of the wire are as follows:
[0054] Provide electrical conductors;
[0055] A dense ceramic film is coated on the surface of the conductor by thermal spraying, vacuum ion plating or vacuum sputtering to form the insulating surface layer. This method can make the insulating surface layer of the wire a ceramic layer, so as to withstand the high temperature environment. Using thermal spraying, vacuum ion plating, vacuum sputtering, etc., a dense ceramic film is covered on the surface of the conductor, such as a layer of zirconium dioxide, aluminum oxide, etc. as an insulating surface layer. Zirconium dioxide can withstand high temperatures of 2200°C. Aluminum oxide can withstand a high temperature of 2050°C, so that the wire can achieve high temperature resistance.
[0056] Further, see figure 1 As a...
Embodiment 2
[0066] Please refer to figure 2 Now the rotor provided by the present invention will be described. The rotor includes a rotating shaft 21 and a high temperature resistant winding 10 mounted on the rotating shaft 21. The high temperature resistant winding 10 is manufactured using the above-mentioned manufacturing method of the high temperature resistant winding.
[0067] The high temperature resistant winding 10 includes a coil 11 and a potting entity 12, and the coil 11 is supported and fixed by the potting entity 12. The coil 11 is made of high-temperature resistant wire. The wire includes a conductor and an insulating surface layer. The insulating surface layer is wrapped on the conductor; the conductor is made of conductive metal for good conduction; the insulating surface is made of inorganic insulating materials for insulation , While achieving high temperature resistance. The potting entity 12 is solidified and molded with inorganic insulating materials, so that it can w...
PUM
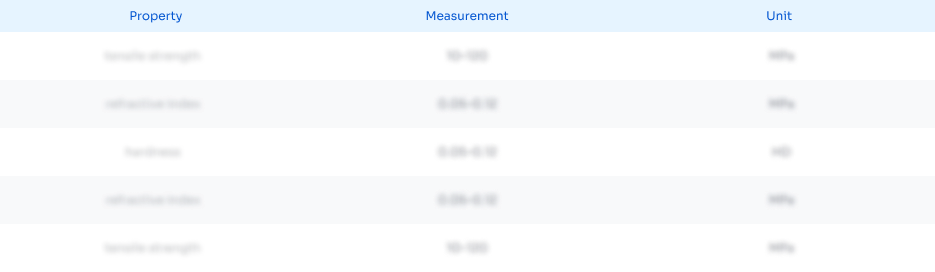
Abstract
Description
Claims
Application Information

- R&D Engineer
- R&D Manager
- IP Professional
- Industry Leading Data Capabilities
- Powerful AI technology
- Patent DNA Extraction
Browse by: Latest US Patents, China's latest patents, Technical Efficacy Thesaurus, Application Domain, Technology Topic, Popular Technical Reports.
© 2024 PatSnap. All rights reserved.Legal|Privacy policy|Modern Slavery Act Transparency Statement|Sitemap|About US| Contact US: help@patsnap.com