A method for utilizing waste heat of fluidized bed coal coke powder
A technology of coal coke powder and fluidized bed, which is applied in the field of pulverized coal fluidized bed pyrolysis and carbonization, can solve the problems of affecting transportation and heat transfer, coal particle heat transfer, coal coke powder is easy to agglomerate, etc., and achieves the realization of utilization Effect
- Summary
- Abstract
- Description
- Claims
- Application Information
AI Technical Summary
Problems solved by technology
Method used
Image
Examples
Embodiment approach 1
[0027] Such as Figure 1-2 As shown, the waste heat utilization method of coal coke powder of the present invention is made up of high-temperature steam production and medium preheating part, carries out coal coke powder cooling and waste heat utilization in cooler 1, and cooler 1 is provided with steam production part housing 14, cooling The shell 14-1 of the medium preheating part and the bottom head 4; the high-temperature coal coke powder 5 enters the steam production part 11 for fluidization through the coal coke powder inlet pipe 111, and the evaporation pipe 2 is arranged in the steam production part 11, and the high-temperature coal coke powder 5. The heat is transferred to the steam-producing part in the evaporating tube through the evaporating tube 2 to supply water C to generate steam D, and the coal coke powder after steam-producing and releasing heat to lower the temperature enters the cooling medium preheating part 12. The water-steam mixture is directly subjected ...
Embodiment approach 2
[0034] Such as image 3 As shown, the coal coke powder waste heat utilization method of the present invention is composed of high-temperature steam production and medium preheating part, and the cooling medium preheating part 12 is arranged on the steam production part 11 outside the steam production part shell 14 and the cooling medium preheating part shell 14-1 is a split structure setting; the coal coke powder cooled in the steam producing part 11 passes through the conveying pipe 114 and then enters the cooling medium preheating part 12 to cool down;
[0035] The circulating water heat exchange tubes 3 in the cooling medium preheating part 12 are grouped into the cooling medium preheating part 12 directly through the bottom head 4; the cooling medium preheating part 12 is also provided with a second fluidizing gas discharge pipe 125; the cooling fluidizing medium 7 enters the cooling medium preheating part 12, controls the heat exchange of the cooling medium preheating par...
Embodiment 1
[0038] Such as figure 1 The method for utilizing waste heat of coal coke powder after dry distillation of a certain coal is shown. The inlet temperature of high-temperature coal coke powder is 600°C, the flow rate is 100t / h, and the outlet temperature is 150°C; Water (temperature 65°C), producing 1.0MPa steam 25t / h; the cooling medium preheating part takes the heat medium, that is, the circulating water at 32°C, and the temperature of the circulating water after heat exchange is 65°C. Nitrogen is used for the fluidization gas of the steam production part and the circulating water preheating part; the diameter of the main shell of the equipment is 2800mm, and the total height is 20m.
[0039] The high-temperature coal coke powder at 600°C first enters the steam production part, and under the action of steam fluidization, it exchanges heat with the circulating water in the evaporation tube. Next, it exchanges heat with the circulating water in the circulating water heat exchang...
PUM
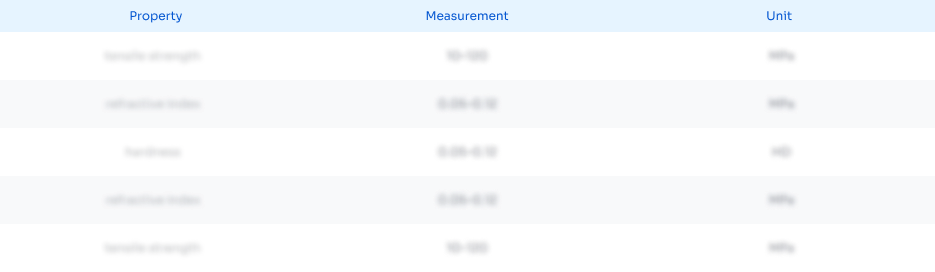
Abstract
Description
Claims
Application Information

- Generate Ideas
- Intellectual Property
- Life Sciences
- Materials
- Tech Scout
- Unparalleled Data Quality
- Higher Quality Content
- 60% Fewer Hallucinations
Browse by: Latest US Patents, China's latest patents, Technical Efficacy Thesaurus, Application Domain, Technology Topic, Popular Technical Reports.
© 2025 PatSnap. All rights reserved.Legal|Privacy policy|Modern Slavery Act Transparency Statement|Sitemap|About US| Contact US: help@patsnap.com