A two-dimensional constant force micro positioning platform based on compliant mechanism
A compliant mechanism and constant force technology, applied in the field of precision micro-operation, can solve the problems of precision influence, poor ability to resist impact load, etc., and achieve the effects of improving positioning accuracy, easy processing and manufacturing, and simple structure
- Summary
- Abstract
- Description
- Claims
- Application Information
AI Technical Summary
Problems solved by technology
Method used
Image
Examples
Embodiment Construction
[0021] The two-dimensional constant force micro-positioning platform of the present invention will be further described in detail below in conjunction with the accompanying drawings and specific embodiments, but it is not intended to limit the present invention.
[0022] Such as figure 1 As shown, the present invention provides a two-dimensional constant force platform 1 for providing constant force output in a specified direction in a two-dimensional plane, including a force input end 3, a force output end 4, a guiding mechanism, a decoupling mechanism and a constant force The force mechanism also includes a base 2. ,
[0023] The guiding mechanism includes a first guiding mechanism 5 in the x direction and a second guiding mechanism 6 in the y direction; the decoupling mechanism includes a first decoupling mechanism 7 in the x direction and a second decoupling mechanism in the y direction Mechanism 8, the first decoupling mechanism 7 is symmetrically distributed about the ...
PUM
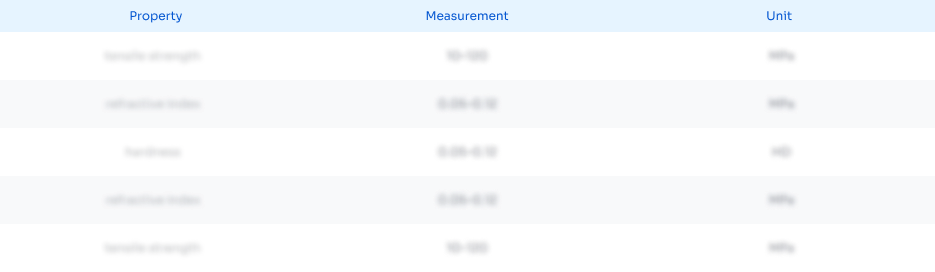
Abstract
Description
Claims
Application Information

- R&D
- Intellectual Property
- Life Sciences
- Materials
- Tech Scout
- Unparalleled Data Quality
- Higher Quality Content
- 60% Fewer Hallucinations
Browse by: Latest US Patents, China's latest patents, Technical Efficacy Thesaurus, Application Domain, Technology Topic, Popular Technical Reports.
© 2025 PatSnap. All rights reserved.Legal|Privacy policy|Modern Slavery Act Transparency Statement|Sitemap|About US| Contact US: help@patsnap.com