Two-dimensional constant force mechanism and positioning platform with the mechanism
A two-dimensional plane, constant force technology, applied to the parts and instruments of the instrument, can solve the problems of difficult and high-precision positioning, difficult to manufacture cost, unable to effectively complete the injection, etc., to achieve easy processing and simple structure. Effect
- Summary
- Abstract
- Description
- Claims
- Application Information
AI Technical Summary
Problems solved by technology
Method used
Image
Examples
Embodiment Construction
[0037] The two-dimensional constant force mechanism and the positioning platform with the mechanism of the present invention will be described in further detail below in conjunction with the accompanying drawings and specific embodiments, but this is not intended to limit the present invention.
[0038] Such as figure 1 As shown, the present invention provides a two-dimensional constant force mechanism 1, which is used to provide a constant force output in a specified direction in a two-dimensional plane, including a force input terminal 3, a force output terminal 4 and a mechanism for connecting the two and conducting the action. The force-transmitting member of the force, also comprising the base 2, and,
[0039] The force transmission member includes a first transmission member 7 that transmits force to the force output end 4 in the first direction and a second transmission member 8 that transmits force to the force output end 4 in the second direction;
[0040] The force in...
PUM
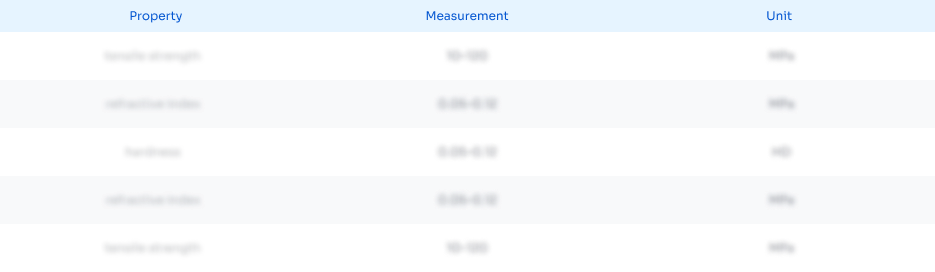
Abstract
Description
Claims
Application Information

- R&D Engineer
- R&D Manager
- IP Professional
- Industry Leading Data Capabilities
- Powerful AI technology
- Patent DNA Extraction
Browse by: Latest US Patents, China's latest patents, Technical Efficacy Thesaurus, Application Domain, Technology Topic, Popular Technical Reports.
© 2024 PatSnap. All rights reserved.Legal|Privacy policy|Modern Slavery Act Transparency Statement|Sitemap|About US| Contact US: help@patsnap.com