Creeping robot driven by shape memory alloy
A memory alloy and memory alloy spring technology, applied in the field of robotics, can solve the problems of limited operating ability, complex control, and few driving forms, and achieve the effects of improving adaptability, small size, and simple structure design and production.
- Summary
- Abstract
- Description
- Claims
- Application Information
AI Technical Summary
Problems solved by technology
Method used
Image
Examples
Embodiment approach
[0022] see Figure 1 , the selected SMA spring of the present invention is that diameter is 4.7mm, and wire diameter is 0.7mm, and the SMA spring that initial length is 30mm is stretched to 90mm, can measure the relationship diagram of energization time and generation force to it energization heating.
[0023] see figure 2 , the peristaltic robot made by the present invention is mainly composed of a silicone body 1 , an SMA spring 2 and a PEEK plate 3 in structure. see image 3 , the SMA spring 2 is inserted into the through hole in the PEEK plate 3, three PEEK plates 3 need to be arranged on the silicone body 1, and the SMA spring 2 is constrained in the groove of the silicone body 1.
[0024] The steps of the method of the present invention are described in detail below.
[0025] The specific implementation steps of the inventive method are as follows:
[0026] Step 1: Referring to the creatures with peristaltic movement in nature, in order to make the body of the robot...
PUM
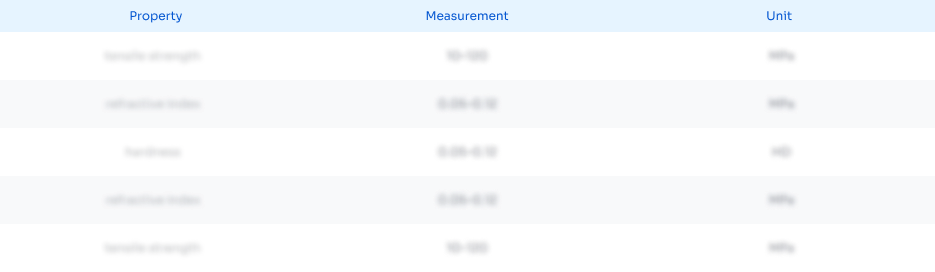
Abstract
Description
Claims
Application Information

- R&D
- Intellectual Property
- Life Sciences
- Materials
- Tech Scout
- Unparalleled Data Quality
- Higher Quality Content
- 60% Fewer Hallucinations
Browse by: Latest US Patents, China's latest patents, Technical Efficacy Thesaurus, Application Domain, Technology Topic, Popular Technical Reports.
© 2025 PatSnap. All rights reserved.Legal|Privacy policy|Modern Slavery Act Transparency Statement|Sitemap|About US| Contact US: help@patsnap.com