Manufacturing process of concrete board shell with shape being digitally generated
A manufacturing process, concrete technology, applied in the field of digital raw concrete slab and shell manufacturing process, can solve the problems of reducing the bearing capacity of components, destroying structural safety, discounting tensile performance and bending resistance, and achieving the elimination of slab shells The effect of reducing the bearing capacity, reducing the amount of cement, and improving the strength of concrete
- Summary
- Abstract
- Description
- Claims
- Application Information
AI Technical Summary
Problems solved by technology
Method used
Image
Examples
Embodiment
[0024] The digital raw concrete slab and shell manufacturing process of this embodiment is used to generate figure 1 The arched shell structure shown includes the following steps:
[0025] 1) Modeling the formwork support 2 of the plate shell, manufacturing and installing the formwork support 2 of the plate shell by using digital modeling technology, and the final formed formwork support 2 is composed of several support units connected to each other.
[0026] After the design shape of the plate shell is known, the shape of the formwork support can be easily obtained through the existing technology, for example, it can be obtained according to the predetermined thickness extending downward and inward from the lower surface of the plate shell.
[0027] Formwork supports of almost any shape can be generated by digital prototyping technology, such as Figure 4 The profiled shape shown. The bracket units are preferably Y-shaped units, and the bracket units are connected to each o...
PUM
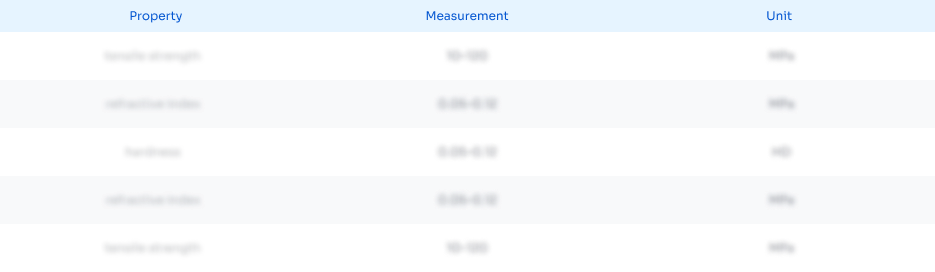
Abstract
Description
Claims
Application Information

- Generate Ideas
- Intellectual Property
- Life Sciences
- Materials
- Tech Scout
- Unparalleled Data Quality
- Higher Quality Content
- 60% Fewer Hallucinations
Browse by: Latest US Patents, China's latest patents, Technical Efficacy Thesaurus, Application Domain, Technology Topic, Popular Technical Reports.
© 2025 PatSnap. All rights reserved.Legal|Privacy policy|Modern Slavery Act Transparency Statement|Sitemap|About US| Contact US: help@patsnap.com