Stone-imitating coating and preparation method thereof
A stone-like coating and emulsion technology, applied in the coating and other directions, can solve the problems of complex preparation process, various components, poor stability, etc., and achieve the effect of optimizing process parameters, good economic benefits, and good stability
- Summary
- Abstract
- Description
- Claims
- Application Information
AI Technical Summary
Problems solved by technology
Method used
Image
Examples
Embodiment 1
[0089] 1. Prepare protective glue solution:
[0090] Put deionized water and protective glue into the mixer at a ratio of 4:1, stir and disperse at 460 rpm for 30 minutes, and store for later use.
[0091] 2. Prepare the dispersed phase:
[0092] (1) Stir the above-mentioned deionized water and cellulose in a disperser for 15 minutes at a speed of 1000 r / min. Get the first mixture;
[0093] (2) Add dispersant, defoamer, propylene glycol, pH regulator, film forming aid, emulsion, and preservative to the second mixture under the condition of 460r / min;
[0094] (3) Adding thickener and protective gum solution to the second mixture under the condition of 1000r / min to obtain the third mixture;
[0095] (4) Add sintered colored sand to the third mixture under the condition of 460r / min to obtain the dispersed phase;
[0096] The dispersed phase includes the following components in parts by weight: 300 parts of deionized water, 2 parts of dispersant, 8 parts of cellulose, 6 parts of antifoaming ...
Embodiment 2
[0106] 1. Prepare protective glue solution:
[0107] Put the deionized water and the protective glue into the mixer at a ratio of 7:1, stir and disperse at 400 rpm for 30 minutes, and store for later use.
[0108] 2. Prepare the dispersed phase:
[0109] (1) Stir the deionized water and cellulose in a disperser for 15 minutes at a speed of 800 r / min. Get the first mixture;
[0110] (2) Add dispersant, defoamer, propylene glycol, PH regulator, film forming aid, emulsion, preservative to the second mixture under the condition of 400r / min for the first mixture;
[0111] (3) Adding thickener and protective gum solution to the second mixture under the condition of 800r / min to obtain the third mixture;
[0112] (4) Add sintered colored sand to the third mixture under the condition of 400r / min to obtain the dispersed phase;
[0113] The dispersed phase includes the following components in parts by weight: 200 parts of deionized water, 1 part of dispersant, 5 parts of cellulose, 2 parts of antif...
Embodiment 3
[0124] 1. Prepare protective glue solution:
[0125] Put the deionized water and the protective glue into the mixer at a ratio of 3:1, stir and disperse at 500 rpm for 30 minutes, and store for later use.
[0126] 2. Prepare the dispersed phase:
[0127] (1) Stir the deionized water and cellulose in the disperser for 15 minutes at a speed of 1500 r / min. Get the first mixture;
[0128] (2) Add dispersant, defoamer, propylene glycol, PH regulator, film forming aid, emulsion, and preservative to the second mixture under the condition of 500r / min;
[0129] (3) Adding thickener and protective gum solution to the second mixture under the condition of 1500r / min to obtain the third mixture;
[0130] (4) The third mixture is added with sintered colored sand under the condition of 500r / min to obtain the dispersed phase;
[0131] The dispersed phase includes the following components in parts by weight: 400 parts of deionized water, 3 parts of dispersant, 10 parts of cellulose, 8 parts of antifoamin...
PUM
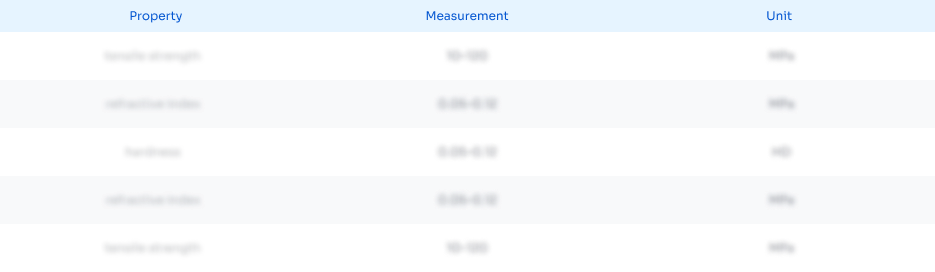
Abstract
Description
Claims
Application Information

- R&D
- Intellectual Property
- Life Sciences
- Materials
- Tech Scout
- Unparalleled Data Quality
- Higher Quality Content
- 60% Fewer Hallucinations
Browse by: Latest US Patents, China's latest patents, Technical Efficacy Thesaurus, Application Domain, Technology Topic, Popular Technical Reports.
© 2025 PatSnap. All rights reserved.Legal|Privacy policy|Modern Slavery Act Transparency Statement|Sitemap|About US| Contact US: help@patsnap.com