Preparation method of hydrophobic material based on silica
A technology of silica, hydrophobic material, applied in coating and other directions, can solve problems such as poor durability and wear resistance
- Summary
- Abstract
- Description
- Claims
- Application Information
AI Technical Summary
Problems solved by technology
Method used
Examples
preparation example Construction
[0020] The invention discloses a preparation method based on silicon dioxide hydrophobic material, and the preparation method comprises the following steps:
[0021] (1) Using ethyl orthosilicate as a raw material, add absolute ethanol, stir for 20-40 minutes, then add ammonia water to adjust the pH of the reaction solution to 8-10, and continue stirring for 1-2 hours to obtain a silica suspension;
[0022] (2) Add absolute ethanol to the above silicon dioxide suspension, sonicate for 1-2 hours, then add a certain amount of stearic acid, continue to sonicate for 20-40 minutes, and then put the ultrasonic mixture at 65-75°C Stir magnetically for 8-12 hours, stir at room temperature for 5-8 hours, and prepare the product for later use. Each 1L of the mixture contains 50-100g of stearic acid;
[0023] (3) Add a certain amount of absolute ethanol to the product obtained in step (2), stir evenly, and then apply the resulting mixture to the surface of the pretreated metal substrate,...
Embodiment 1
[0029] (1) Using ethyl orthosilicate as a raw material, add absolute ethanol, stir for 20 minutes, then add ammonia water to adjust the pH value of the reaction solution to 8, continue stirring for 1 hour, and obtain a silica suspension with a concentration of 0.1 g / mL, Wherein, the mass ratio of described ethyl orthosilicate, described dehydrated alcohol, described ammoniacal liquor is 40:100:3;
[0030] (2) Add absolute ethanol to the above silica suspension, sonicate for 1h, then add a certain amount of stearic acid, continue to sonicate for 20min, then magnetically stir the mixture after sonication at 65°C for 8h, and stir at room temperature 5h, the product is ready for use, wherein, every 1L of the mixed solution contains 50g of stearic acid;
[0031] (3) Add the same volume of absolute ethanol to the product obtained in step (2), stir evenly, then coat the resulting mixture on the surface of the pretreated metal substrate, volatilize the solvent at 90°C, and then Dry a...
Embodiment 2
[0033] (1) Using ethyl orthosilicate as raw material, add absolute ethanol, stir for 30 minutes, then add ammonia water to adjust the pH value of the reaction solution to 9, continue stirring for 1.5 hours, and obtain a silica suspension with a concentration of 0.5g / mL , wherein, the mass ratio of described ethyl orthosilicate, described dehydrated alcohol, described ammoniacal liquor is 45:110:6;
[0034] (2) Add absolute ethanol to the above silicon dioxide suspension, sonicate for 1.5h, then add a certain amount of stearic acid, continue to sonicate for 30min, then magnetically stir the mixture after sonication at 70°C for 10h, room temperature Stir for 6 hours, and the product is set aside, wherein, every 1L of the mixed solution contains 70g of stearic acid;
[0035] (3) Add the same volume of absolute ethanol to the product obtained in step (2), stir evenly, then coat the resulting mixture on the surface of the pretreated metal substrate, volatilize the solvent at 90°C, ...
PUM
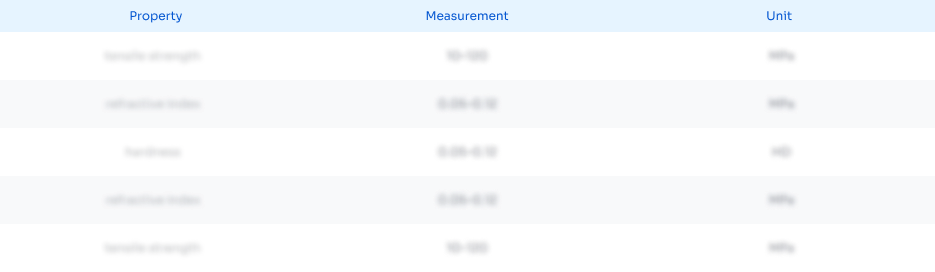
Abstract
Description
Claims
Application Information

- R&D Engineer
- R&D Manager
- IP Professional
- Industry Leading Data Capabilities
- Powerful AI technology
- Patent DNA Extraction
Browse by: Latest US Patents, China's latest patents, Technical Efficacy Thesaurus, Application Domain, Technology Topic, Popular Technical Reports.
© 2024 PatSnap. All rights reserved.Legal|Privacy policy|Modern Slavery Act Transparency Statement|Sitemap|About US| Contact US: help@patsnap.com