Manufacturing process of carbon plastic plate with high flame resistance
A manufacturing process and high flame-retardant technology, which is applied in the field of high flame-retardant carbon-plastic plate manufacturing process, can solve the problems of poor flame-retardant performance, achieve good flame-retardant effect, reduce usage, and improve enrichment efficiency
- Summary
- Abstract
- Description
- Claims
- Application Information
AI Technical Summary
Problems solved by technology
Method used
Image
Examples
Embodiment 1
[0022] A manufacturing process for a high flame-retardant carbon-plastic panel disclosed in Example 1 includes the following preparation steps:
[0023] 1) According to the number of parts by mass, take 500 parts of bamboo charcoal particles with a pore size of 0.05 mm, 200 parts of carbonized coconut shell powder, and 40 parts of shell powder, add 400 parts of NaOH and soak for 12 hours, filter and remove the solution, wash 3 times with deionized water, add 100 parts of One part of deionized water was mixed and stirred to dissolve to obtain the mixed base material A;
[0024] Wherein the preparation method of carbonized coconut shell powder is:
[0025] A. Put the coconut shell into the carbonization equipment and go through drying treatment to remove 99.9% of the water, then raise the temperature to 210℃~230℃ for preheating, and then heat the temperature to 800-1100℃ for deep carbonization treatment; in helium Protected and cooled to 60°C, crushed to 1-5mm carbonized coconu...
Embodiment 2
[0032] A manufacturing process for a highly flame-retardant carbon-plastic panel disclosed in Example 2 includes the following preparation steps:
[0033] 1) According to the number of parts by mass, take 450 parts of bamboo charcoal particles with a pore size of 0.05 mm, 50 parts of carbonized coconut shell powder, and 10 parts of shell powder, add 400 parts of NaOH to soak for 12 hours, filter to remove the solution, wash 3 times with deionized water, add 100 parts One part of deionized water was mixed and stirred to dissolve to obtain the mixed base material A;
[0034] Wherein the preparation method of carbonized coconut shell powder is:
[0035] A. Put the coconut shell into the carbonization equipment and go through drying treatment to remove 99.9% of the water, then raise the temperature to 210℃~230℃ for preheating, and then heat the temperature to 800-1100℃ for deep carbonization treatment; in helium Protected and cooled to 60°C, crushed to 1-5mm carbonized coconut sh...
Embodiment 3
[0042] A manufacturing process for a highly flame-retardant carbon-plastic panel disclosed in Example 3 includes the following preparation steps:
[0043] 1) According to the number of parts by mass, take 550 parts of bamboo charcoal particles with a pore size of 0.05 mm, 100 parts of carbonized coconut shell powder, and 30 parts of shell powder, add 400 parts of NaOH to soak for 12 hours, filter and remove the solution, wash 3 times with deionized water, add 100 parts of One part of deionized water was mixed and stirred to dissolve to obtain the mixed base material A;
[0044] Wherein the preparation method of carbonized coconut shell powder is:
[0045] A. Put the coconut shell into the carbonization equipment and go through drying treatment to remove 99.9% of the water, then raise the temperature to 210℃~230℃ for preheating, and then heat the temperature to 800-1100℃ for deep carbonization treatment; in helium Protected and cooled to 60°C, crushed to 1-5mm carbonized cocon...
PUM
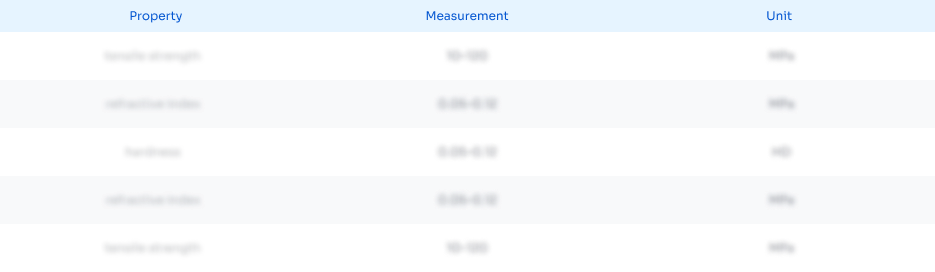
Abstract
Description
Claims
Application Information

- R&D
- Intellectual Property
- Life Sciences
- Materials
- Tech Scout
- Unparalleled Data Quality
- Higher Quality Content
- 60% Fewer Hallucinations
Browse by: Latest US Patents, China's latest patents, Technical Efficacy Thesaurus, Application Domain, Technology Topic, Popular Technical Reports.
© 2025 PatSnap. All rights reserved.Legal|Privacy policy|Modern Slavery Act Transparency Statement|Sitemap|About US| Contact US: help@patsnap.com