Mold release agent for wood-plastic composite material
A wood-plastic composite material and release agent technology, which is applied in the field of polymer materials, can solve the problems of short service life of release agent and poor release effect, so as to prolong service life, improve release effect and reduce peeling force Effect
- Summary
- Abstract
- Description
- Claims
- Application Information
AI Technical Summary
Problems solved by technology
Method used
Image
Examples
example 1
[0024] In parts by weight, put 5 parts of hydroxypropyl methylcellulose, 5 parts of polyvinyl alcohol, and 100 parts of water in a beaker, stir with a glass rod for 30 minutes, let it stand for swelling for 5 hours, and place the beaker on a digital display to measure the speed. In a constant temperature magnetic stirrer, at a temperature of 85°C, heat, stir and mix for 60 minutes to obtain an aqueous dispersant solution; in parts by weight, 10 parts of plasticizer, 5 parts of phospholipid, 8 parts of emulsifier, and 10 parts of aqueous solution of dispersant , 10 parts of pretreated dicyclohexyl peroxydicarbonate, 300 parts of water, water is added to the polymerization kettle, the temperature is raised to 50 ° C, and then plasticizer, phospholipid, emulsifier, dispersant aqueous solution are added to the polymerization kettle, To pretreat dicyclohexyl peroxydicarbonate, stir and mix for 30min at a temperature of 50°C and a rotational speed of 500r / min, then feed nitrogen gas ...
example 2
[0026]In parts by weight, put 5 parts of hydroxypropyl methylcellulose, 5 parts of polyvinyl alcohol, and 100 parts of water in a beaker, stir with a glass rod for 30 minutes, let it stand for swelling for 5 hours, and place the beaker on a digital display to measure the speed. In a constant temperature magnetic stirrer, at a temperature of 85°C, heat, stir and mix for 60 minutes to obtain an aqueous dispersant solution; in parts by weight, 10 parts of plasticizer, 5 parts of phospholipid, 8 parts of emulsifier, and 10 parts of aqueous solution of dispersant , 10 parts of dicyclohexyl peroxydicarbonate, 300 parts of water, add water to the polymerization kettle, raise the temperature to 50 ° C, then add plasticizer, phospholipid, emulsifier, dispersant aqueous solution, peroxide Dicyclohexyl dicarbonate, at a temperature of 50°C and a rotational speed of 500r / min, stir and mix for 30min, then feed nitrogen containing vinyl chloride into the polymerization tank at a rate of 90mL...
example 3
[0028] In parts by weight, put 5 parts of hydroxypropyl methylcellulose, 5 parts of polyvinyl alcohol, and 100 parts of water in a beaker, stir with a glass rod for 30 minutes, let it stand for swelling for 5 hours, and place the beaker on a digital display to measure the speed. In a constant temperature magnetic stirrer, at a temperature of 85°C, heat, stir and mix for 60 minutes to obtain an aqueous solution of a dispersant; in parts by weight, 10 parts of a plasticizer, 8 parts of an emulsifier, 10 parts of an aqueous solution of a dispersant, and 10 parts of a pre- Treat dicyclohexyl peroxydicarbonate, 300 parts of water, add water to the polymerization kettle, heat up to 50°C, then add plasticizer, emulsifier, dispersant aqueous solution to the polymerization kettle, pretreatment of dicarbonic acid peroxide Dicyclohexyl ester, at a temperature of 50°C and a rotational speed of 500r / min, stir and mix for 30min, then feed nitrogen containing vinyl chloride into the polymeriz...
PUM
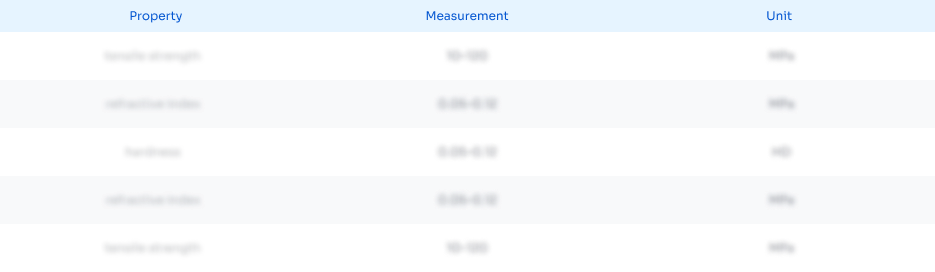
Abstract
Description
Claims
Application Information

- Generate Ideas
- Intellectual Property
- Life Sciences
- Materials
- Tech Scout
- Unparalleled Data Quality
- Higher Quality Content
- 60% Fewer Hallucinations
Browse by: Latest US Patents, China's latest patents, Technical Efficacy Thesaurus, Application Domain, Technology Topic, Popular Technical Reports.
© 2025 PatSnap. All rights reserved.Legal|Privacy policy|Modern Slavery Act Transparency Statement|Sitemap|About US| Contact US: help@patsnap.com