Flexible operating arm elastic vibration suppression method based on frequency characteristic identification
A technology of elastic vibration and frequency characteristics, applied in the direction of adaptive control, general control system, control/regulation system, etc., can solve the problems of lack of self-adaptive ability and poor vibration suppression effect, so as to improve operation safety and save energy. Cost, effect of high adaptability
- Summary
- Abstract
- Description
- Claims
- Application Information
AI Technical Summary
Problems solved by technology
Method used
Image
Examples
Embodiment Construction
[0032] In order to make the technical means, creative features, goals and effects achieved by the present invention easy to understand, the present invention will be further elaborated below.
[0033] In order to illustrate the present invention more clearly, as figure 2 As shown, a specific system using the method of the present invention is preferred, including a servo motor 1, a coupling 2, a slider 3, a bolt 4, a moving guide rail 5, an end load 6, a flexible operating arm 7, a ball screw pair 8, Frequency feature recognition module 9 , elastic vibration feedforward adaptive controller 11 , convolution module 12 , motion control card 14 , motor driver 15 .
[0034] Among them, the servo motor 1 is connected with the ball screw pair 8 through the coupling 2 and then drives the slider 3 to move on the moving guide rail 5. One end of the flexible operating arm 7 is rigidly connected with the slider 3 through the bolt 4, and the other end operates the end load 6. According ...
PUM
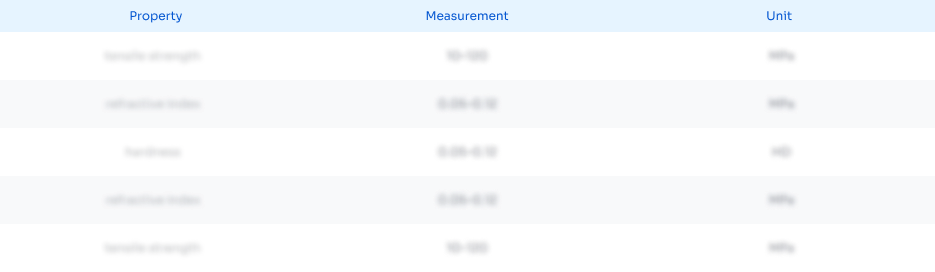
Abstract
Description
Claims
Application Information

- Generate Ideas
- Intellectual Property
- Life Sciences
- Materials
- Tech Scout
- Unparalleled Data Quality
- Higher Quality Content
- 60% Fewer Hallucinations
Browse by: Latest US Patents, China's latest patents, Technical Efficacy Thesaurus, Application Domain, Technology Topic, Popular Technical Reports.
© 2025 PatSnap. All rights reserved.Legal|Privacy policy|Modern Slavery Act Transparency Statement|Sitemap|About US| Contact US: help@patsnap.com