Instrument panel heat insulation anti-reflective film and preparation method thereof
An anti-reflective and instrument panel technology, which is applied in the field of heat-insulating anti-reflective film for instrument panels and its preparation, can solve problems such as allergic reactions of allergic people, lack of air purification, troublesome cleaning, etc., and achieve improved brightness, strong adsorption capacity, and improved The effect of adsorption capacity
- Summary
- Abstract
- Description
- Claims
- Application Information
AI Technical Summary
Problems solved by technology
Method used
Image
Examples
Embodiment 1
[0020] A heat-insulating anti-reflection film for an instrument panel, the components by weight are as follows: 20 parts of hollow alumina modified resin, 5 parts of inorganic filler, 5 parts of ceramic powder, 5 parts of sodium carboxymethyl cellulose, 5 parts of glycerin, carapace 5 parts of quality, 30 parts of 20% acetic acid, 5 parts of sodium lauryl sulfate, and 5 parts of silane coupling agent.
[0021] Preferably, the inorganic filler is prepared from nano-titanium dioxide, nano-silicon dioxide and nano-glass microspheres in a weight ratio of 1:1:2.
[0022] A method for preparing a heat-insulating anti-reflection film for an instrument panel, the specific steps are as follows:
[0023] 1) Take 20 parts of polyurethane resin and 15 parts of epoxy resin and mix them evenly, then add 20 parts of dimethylformamide, and carry out heating reaction. The heating temperature is 200°C, and the reaction time is 30 minutes. Slowly add 5 parts of polyethylene glycol dropwise, the...
Embodiment 2
[0032] A heat-insulating and anti-reflective film for an instrument panel. The components are as follows in parts by weight: 30 parts of hollow alumina modified resin, 7 parts of inorganic filler, 10 parts of ceramic powder, 7 parts of sodium carboxymethyl cellulose, 7 parts of glycerin, 10 parts of chitin, 40 parts of 20% acetic acid, 10 parts of sodium lauryl sulfate, and 7 parts of silane coupling agent.
[0033] Preferably, the inorganic filler is prepared from nano-titanium dioxide, nano-silicon dioxide and nano-glass microspheres in a weight ratio of 1:2:2.
[0034] A method for preparing a heat-insulating anti-reflection film for an instrument panel, the specific steps are as follows:
[0035]1) Take 25 parts of polyurethane resin and 20 parts of epoxy resin, mix them evenly, add 30 parts of dimethylformamide, and carry out heating reaction. The heating temperature is 220°C, and the reaction time is 40 minutes. Slowly add 10 parts of polyethylene glycol dropwise, the d...
Embodiment 3
[0044] A heat-insulating and anti-reflective film for an instrument panel. The components are as follows in parts by weight: 50 parts of hollow alumina modified resin, 10 parts of inorganic filler, 15 parts of ceramic powder, 10 parts of sodium carboxymethyl cellulose, 10 parts of glycerin, 15 parts of chitin, 50 parts of 30% acetic acid, 15 parts of sodium lauryl sulfate, and 10 parts of silane coupling agent.
[0045] Preferably, the inorganic filler is prepared from nano-titanium dioxide, nano-silicon dioxide and nano-glass microspheres in a weight ratio of 1:2:3.
[0046] A method for preparing a heat-insulating anti-reflection film for an instrument panel, the specific steps are as follows:
[0047] 1) Take 30 parts of polyurethane resin and 25 parts of epoxy resin and mix them evenly, then add 40 parts of dimethylformamide, and carry out heating reaction. The heating temperature is 240°C, and the reaction time is 50 minutes. Slowly add 15 parts of polyethylene glycol dr...
PUM
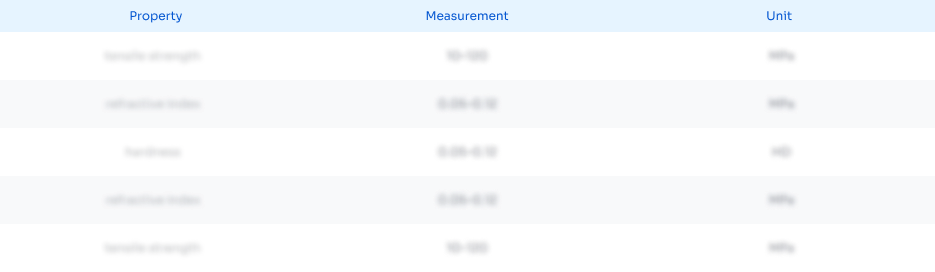
Abstract
Description
Claims
Application Information

- R&D Engineer
- R&D Manager
- IP Professional
- Industry Leading Data Capabilities
- Powerful AI technology
- Patent DNA Extraction
Browse by: Latest US Patents, China's latest patents, Technical Efficacy Thesaurus, Application Domain, Technology Topic, Popular Technical Reports.
© 2024 PatSnap. All rights reserved.Legal|Privacy policy|Modern Slavery Act Transparency Statement|Sitemap|About US| Contact US: help@patsnap.com