Method for synthesizing epoxy-modified silicone resin
A technology of epoxy modification and synthesis method, applied in the field of organosilicon modification, can solve the problems of waste acid water, waste alkali water and waste salt pollution, difficult to obtain expected structural products, etc. Environmentally friendly effect
- Summary
- Abstract
- Description
- Claims
- Application Information
AI Technical Summary
Problems solved by technology
Method used
Examples
Embodiment 1
[0015] Take by weighing 272g of methyltrimethoxysilane, 118g of (3-glycidylpropyl)trimethoxysilane, and 200g of methanol, and add them into a 1000ml four-necked flask with cooling, stirring and heating devices and stir evenly; then weigh fluorine Dissolve 0.5 g of sodium fluoride in 45 g of water, slowly add sodium fluoride aqueous solution to a four-neck flask at 10°C, and continue to react for 1 hour after the addition; then raise the temperature to 40°C for 1 hour, distill under reduced pressure, and filter out fluoride Sodium obtained 250.25 g of colorless transparent epoxy-modified silicone resin.
Embodiment 2
[0017] Weigh in turn 396g of phenyltrimethoxysilane, 47.2g of (3-glycidylpropyl)trimethoxysilane, and 200g of toluene, and add them to a 1000ml four-necked flask with cooling, stirring and heating devices and stir evenly; then weigh Dissolve 0.4g of sodium fluoride in 39.6g of water, slowly add sodium fluoride aqueous solution dropwise to a four-necked flask at 10°C, and continue to react for 1 hour after the dropwise addition; then raise the temperature to 60°C for 2 hours, distill under reduced pressure, and filter out Sodium fluoride was used to obtain 308.48 g of a colorless and transparent epoxy-modified silicone resin.
Embodiment 3
[0019] Sequentially weigh 396g of phenyltrimethoxysilane, 49.2g of 2-(3,4-epoxycyclohexyl)ethyltrimethoxysilane, and 200g of toluene into a 1000ml four-necked flask equipped with cooling, stirring and heating devices Stir evenly; then weigh 0.4g of sodium fluoride and dissolve it in 39.6g of water, slowly add sodium fluoride aqueous solution dropwise to the four-necked flask at 10°C, and continue the reaction for 1h after the addition; then raise the temperature to 60°C and keep it for 2h , distilled under reduced pressure, and filtered off sodium fluoride to obtain 316.82 g of a colorless and transparent epoxy-modified silicone resin.
PUM
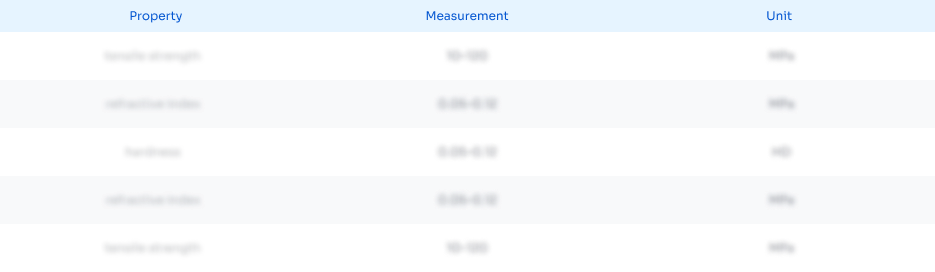
Abstract
Description
Claims
Application Information

- R&D
- Intellectual Property
- Life Sciences
- Materials
- Tech Scout
- Unparalleled Data Quality
- Higher Quality Content
- 60% Fewer Hallucinations
Browse by: Latest US Patents, China's latest patents, Technical Efficacy Thesaurus, Application Domain, Technology Topic, Popular Technical Reports.
© 2025 PatSnap. All rights reserved.Legal|Privacy policy|Modern Slavery Act Transparency Statement|Sitemap|About US| Contact US: help@patsnap.com