Geometric parameter optimization method for ball-end milling cutter based on co-simulation
A technology of geometric parameters and ball-end milling cutters, applied in geometric CAD, design optimization/simulation, electrical digital data processing, etc., can solve problems such as waste of time, high cost, low degree of automation, etc., to reduce optimization costs and meet flexibility , to avoid the effect of repeated simulation modeling
- Summary
- Abstract
- Description
- Claims
- Application Information
AI Technical Summary
Problems solved by technology
Method used
Examples
Embodiment Construction
[0012] In order to make the technical problems, technical solutions and advantages to be solved by the present invention clearer, the following will describe in detail in conjunction with specific embodiments.
[0013] A method for optimizing the geometric parameters of a ball-end milling cutter based on co-simulation is characterized in that it comprises the following steps:
[0014] a. Select UG software to establish a parametric solid model of the ball end milling cutter, compile a C code program to control the parameterized characteristic variables to generate tool models with different geometric parameters and output the model file in stp format;
[0015] b. Select ABAQUS finite element analysis software to establish a 3D milling simulation analysis model, import the tool model file in stp format, set material properties and contact property parameters, and also include cutting depth, cutting speed and feed speed parameter settings, and extract 3D milling simulation Analy...
PUM
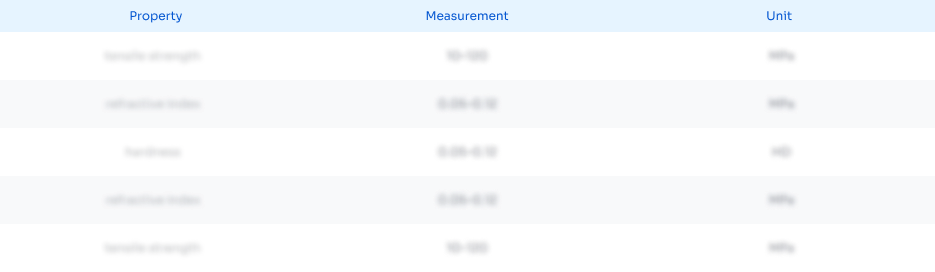
Abstract
Description
Claims
Application Information

- R&D Engineer
- R&D Manager
- IP Professional
- Industry Leading Data Capabilities
- Powerful AI technology
- Patent DNA Extraction
Browse by: Latest US Patents, China's latest patents, Technical Efficacy Thesaurus, Application Domain, Technology Topic, Popular Technical Reports.
© 2024 PatSnap. All rights reserved.Legal|Privacy policy|Modern Slavery Act Transparency Statement|Sitemap|About US| Contact US: help@patsnap.com