Chattering restraining method of optical axis of rapid deflecting mirror based on support vector machine
A support vector machine and support vector technology, applied in adaptive control, general control system, control/regulation system and other directions, can solve the problem of inverse hysteresis model being difficult to obtain, achieve high accuracy of boresight jitter, improve control accuracy, The effect of simplifying the model identification process
- Summary
- Abstract
- Description
- Claims
- Application Information
AI Technical Summary
Problems solved by technology
Method used
Image
Examples
Embodiment Construction
[0047]The present invention will be further described below in conjunction with specific embodiments. The exemplary embodiments and descriptions of the present invention are used to explain the present invention, but not as a limitation to the present invention.
[0048] Such as figure 1 As shown, a support vector machine-based fast deflection mirror boresight chattering suppression method of this embodiment, the specific steps are as follows:
[0049] Modeling and identification of linear dynamics of fast deflecting mirrors. Fast deflecting mirror input u and linear model output represented by fast deflecting mirror linear dynamic model D( ) The relationship between. It can be expressed as
[0050]
[0051] In the formula, k is the constant gain introduced due to the quasi-static rate-independent hysteresis dynamics, θ is the actual output of the fast deflecting mirror, n and m are the order of the model, β i and η i Undetermined parameters for the model.
[0052]...
PUM
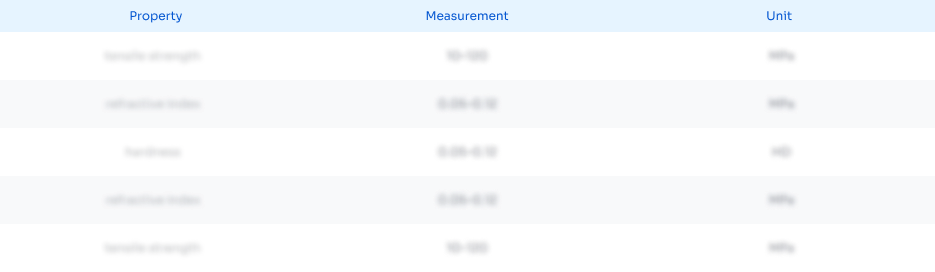
Abstract
Description
Claims
Application Information

- R&D
- Intellectual Property
- Life Sciences
- Materials
- Tech Scout
- Unparalleled Data Quality
- Higher Quality Content
- 60% Fewer Hallucinations
Browse by: Latest US Patents, China's latest patents, Technical Efficacy Thesaurus, Application Domain, Technology Topic, Popular Technical Reports.
© 2025 PatSnap. All rights reserved.Legal|Privacy policy|Modern Slavery Act Transparency Statement|Sitemap|About US| Contact US: help@patsnap.com