A system for eliminating burrs of magnetic displacement sensors in rail status monitoring
A magnetic displacement and sensor technology, which is applied in the system field of eliminating burrs of magnetic displacement sensors in rail status monitoring, can solve problems such as low-level DC signal noise interference, DC level drift, and difficulties, so as to improve measurement accuracy and eliminate Glitches, effects of preventing logic races
- Summary
- Abstract
- Description
- Claims
- Application Information
AI Technical Summary
Problems solved by technology
Method used
Image
Examples
Embodiment 1
[0037] Such as figure 1 As shown, the present embodiment 1 provides a system for eliminating the burr phenomenon of the magnetic displacement sensor during rail state monitoring, and the system is synchronized with a clock; the system includes the following parts that are electrically connected in turn:
[0038] A clock pulse generating module 1, configured to send a start signal and a stop signal for collecting monitoring data to the magnetic displacement sensor group 2, and send a reset signal to the data output module at the end of the monitoring period;
[0039] The magnetic displacement sensor group 2 includes at least two magnetic displacement sensors, which are used to collect displacement change data between bridge slabs, track slabs and rails according to the start signal and the stop signal;
[0040] A data output module, configured to process and serially output the data collected by the magnetic displacement sensor group 2;
[0041] The data output module includes...
Embodiment 2
[0048] Such as figure 2 As shown, on the basis of embodiment 1, this embodiment 2 provides a system for eliminating the burr phenomenon of the magnetic displacement sensor in rail state monitoring. This embodiment 2 further defines the magnetic displacement sensor, the channel counter 3 And there are four format converters 4, and the multiplexer 5 is a four-to-one multiplexer. The four-way magnetic displacement sensors are used to measure the displacement between the two bridge plates, the displacement between the bridge plate and the track plate, the displacement between the left rail and the track plate, and the displacement between the right rail and the track plate, so that the All-round monitoring of rail status.
[0049] The magnetic displacement sensor is a start-stop type magnetic displacement sensor.
[0050] The clock pulse generation module 1 includes a crystal oscillator 11 and a timing reference counter 12 electrically connected in turn, and the crystal oscilla...
Embodiment 3
[0058] Such as image 3 As shown, on the basis of embodiment 1, the present embodiment 3 provides a system for eliminating the burr phenomenon of the magnetic displacement sensor during rail state monitoring. This embodiment 3 further defines that the system is integrated on an FPGA chip, preferably It is the XC3C50AN chip.
PUM
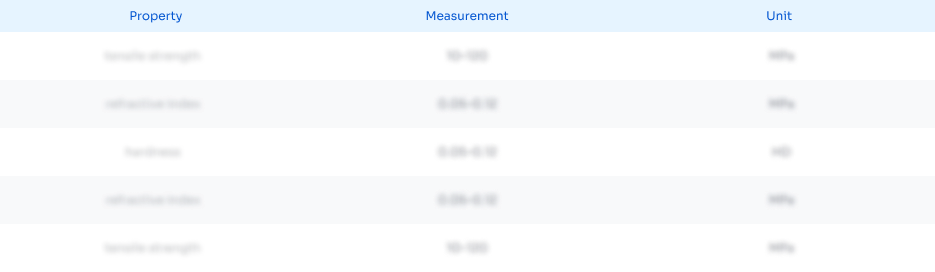
Abstract
Description
Claims
Application Information

- R&D
- Intellectual Property
- Life Sciences
- Materials
- Tech Scout
- Unparalleled Data Quality
- Higher Quality Content
- 60% Fewer Hallucinations
Browse by: Latest US Patents, China's latest patents, Technical Efficacy Thesaurus, Application Domain, Technology Topic, Popular Technical Reports.
© 2025 PatSnap. All rights reserved.Legal|Privacy policy|Modern Slavery Act Transparency Statement|Sitemap|About US| Contact US: help@patsnap.com