Cutter device for improving machining precision of thin and long shaft
A technology of machining precision and slender shaft, which is applied in the direction of tools, manufacturing tools, metal processing equipment, etc. for lathes. The effect of roughness reduction and simplified machine structure
- Summary
- Abstract
- Description
- Claims
- Application Information
AI Technical Summary
Problems solved by technology
Method used
Image
Examples
Embodiment 1
[0030] A tool device for improving the machining accuracy of a slender shaft, its structure is as figure 1 As shown, it includes the blade holder 4 and the blades installed on the blade holder 4. In this embodiment, there are 3 blades, including the first blade 1, the second blade 2, and the third blade 3, which are evenly installed on the blade holder 4. , The three blades are arranged at an interval of 120° in the radial direction, the feed amount of the three blades in the radial direction of the machined part is the same, and the plane formed by the three blades is parallel to the radial plane of the machined part.
[0031] In addition, in this embodiment, the blades are arranged concentrically in the axial direction. The first blade 1, the second blade 2, and the third blade 3 are set to the same cutting depth along the radial direction of the machined part, such as figure 2 As shown, the cutting tips of the three blades are in the same axial position, and the simultaneous c...
Embodiment 2
[0033] A tool device for improving the machining accuracy of a slender shaft. Its structure is roughly the same as that of Embodiment 1. The difference is that the blades in this embodiment adopt an axially offset arrangement, the first blade 1, the second blade 2, the third blade The blade 3 is set with different cutting depths along the radial direction of the machined part. The cutting depths of the three blades along the radial direction of the machined part are gradually deepened. The cutting tips of the three blades are at different positions with a small axial distance. With the same feed, the cutting depth along the radial direction can be different. Under the condition of small deformation, the rough and fine machining of the slender shaft can be completed at the same time, such as Figure 4 and Figure 5 Shown.
[0034] In the above embodiment, the feed amount of the three blades is the same, and the actual feed amount that affects the machining surface accuracy of the...
PUM
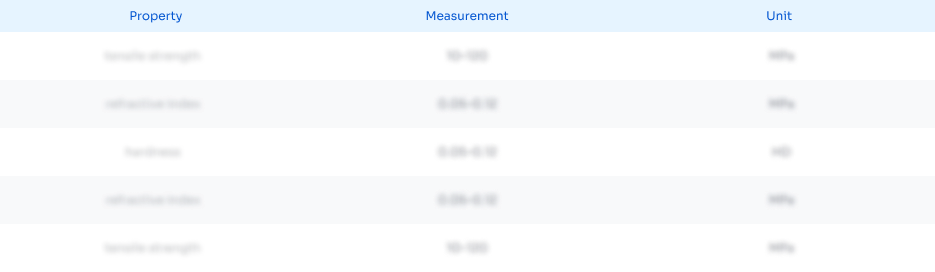
Abstract
Description
Claims
Application Information

- R&D Engineer
- R&D Manager
- IP Professional
- Industry Leading Data Capabilities
- Powerful AI technology
- Patent DNA Extraction
Browse by: Latest US Patents, China's latest patents, Technical Efficacy Thesaurus, Application Domain, Technology Topic, Popular Technical Reports.
© 2024 PatSnap. All rights reserved.Legal|Privacy policy|Modern Slavery Act Transparency Statement|Sitemap|About US| Contact US: help@patsnap.com