Method for calcining Belite sulphoaluminate cement clinker by using phosphogypsum and cement clinker
A technology of special sulfur aluminate and cement clinker, which is applied in the field of cement and can solve problems such as geological disasters, collapse of phosphogypsum slag field, landslides and debris flows
- Summary
- Abstract
- Description
- Claims
- Application Information
AI Technical Summary
Problems solved by technology
Method used
Image
Examples
Embodiment 1
[0040] Place the three raw materials in a drying oven at 100°C and dry them in percentage by weight: phosphogypsum 76.5%, electrolytic aluminum ash 13.3%, and fly ash 10.2%. Weigh 3000g of the mixture and mix it evenly. In the test ball mill, the sieve residue of the 80μm square hole sieve is 8-12%. Add the raw meal powder to 1% tap water, stir evenly and put it into a round grinding tool with an inner diameter of 8 cm and a depth of 2 cm, press it into a cake with a small press, and dry the cake in an oven at 100°C. Take 8 cakes each time, put them into a test electric furnace that is preheated to 1000°C for preheating and desulfurization for 160 minutes, then continue to increase the temperature of the test electric furnace to a temperature of 1350°C, and calcine for 60 minutes until the clinker is mineralized Completely formed. The calcined clinker is blown and cooled to room temperature by a fan.
[0041] After the cooled clinker is crushed, it is ground to a specific surfa...
Embodiment 2
[0048] Place the three raw materials in a drying oven at 100°C and dry them in percentage by weight: phosphogypsum 79.6%, electrolytic aluminum ash 10.1%, and fly ash 10.3%. Weigh 3000g of the mixture and mix it evenly. In the test ball mill, the sieve residue of the 80μm square hole sieve is 8-10%. Add 1% tap water to the raw meal powder, stir evenly and put it into a round grinding tool with an inner diameter of 8cm and a depth of 2cm. Use a small press to form a cake, and place the cake in an oven at 100°C. . Take 8 cakes each time, put them into a test electric furnace that is preheated to 1100°C for preheating and desulfurization for 180 minutes, then continue to increase the temperature of the test electric furnace to a temperature of 1320°C, and calcine for 80 minutes until clinker minerals Completely formed. The calcined clinker is blown and cooled to room temperature by a fan.
[0049] After the cooled clinker is crushed, it is ground to a specific surface area of 4...
Embodiment 3
[0056] Place the three raw materials in a drying box at 100°C and dry them in percentage by weight: phosphogypsum 75.1%, electrolytic aluminum ash 10.0%, and fly ash 14.9%. Weigh 3000g of the mixture and mix it evenly. In the test ball mill, the sieve residue of the 80μm square hole sieve is 8-10%. Add 1% tap water to the raw meal powder, stir evenly and put it into a round grinding tool with an inner diameter of 8cm and a depth of 2cm. Use a small press to form a cake, and place the cake in an oven at 100°C. . Take 8 cakes each time and put them into a test electric furnace that is preheated to 1000°C for preheating and desulfurization for 160 minutes, then continue to increase the temperature of the test electric furnace to a temperature of 1350°C and calcine for 70 minutes until the clinker is mineralized Completely formed. The calcined clinker is blown and cooled to room temperature by a fan.
[0057] After the cooled clinker is crushed, it is ground to a specific surface ...
PUM
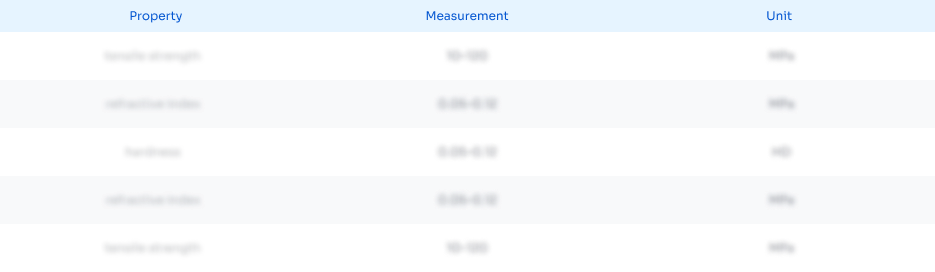
Abstract
Description
Claims
Application Information

- R&D Engineer
- R&D Manager
- IP Professional
- Industry Leading Data Capabilities
- Powerful AI technology
- Patent DNA Extraction
Browse by: Latest US Patents, China's latest patents, Technical Efficacy Thesaurus, Application Domain, Technology Topic, Popular Technical Reports.
© 2024 PatSnap. All rights reserved.Legal|Privacy policy|Modern Slavery Act Transparency Statement|Sitemap|About US| Contact US: help@patsnap.com