Double-drive five-bar slider parallel mechanism CNC machining platform
A processing platform and dual-drive technology, applied in the direction of workbench, metal processing equipment, metal processing machinery parts, etc., can solve the problems of affecting the processing effect, processing accuracy and low efficiency, and achieve compact structure, high processing accuracy and wide working range big effect
- Summary
- Abstract
- Description
- Claims
- Application Information
AI Technical Summary
Problems solved by technology
Method used
Image
Examples
Embodiment Construction
[0032] The specific implementation manner of the present invention will be described below in conjunction with the accompanying drawings.
[0033] as attached figure 1 As shown, the dual-drive five-bar slider parallel mechanism CNC machining platform of this embodiment includes a base plate 1, and two ends of the base plate 1 are respectively fixed with a screw stepping motor 18 and a gear stepping motor 19, which are located at the screw stepping On the substrate 1 between the motor 18 and the gear stepping motor 19, two linear guide rails 9 are respectively installed through two sets of guide rail supports 16, and a screw 8 is arranged between the two linear guide rails 9, and one end of the screw rod 8 is connected through a joint. The shaft device 15 is connected to the output end of the screw stepper motor 18, and the other end is fixed on the base 26 of the base plate 1; there is a chute in the middle of the base plate 1, and the slider base plate 2 sliding along it is i...
PUM
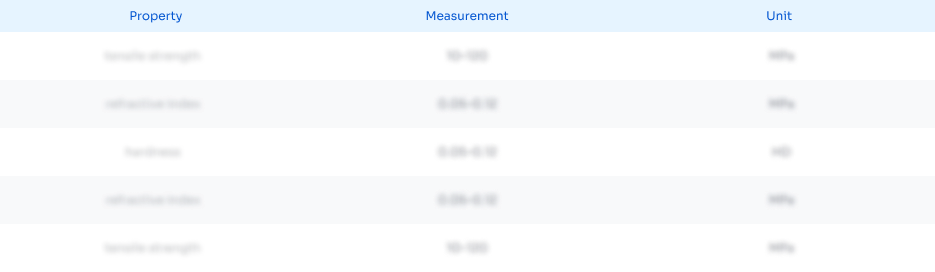
Abstract
Description
Claims
Application Information

- R&D
- Intellectual Property
- Life Sciences
- Materials
- Tech Scout
- Unparalleled Data Quality
- Higher Quality Content
- 60% Fewer Hallucinations
Browse by: Latest US Patents, China's latest patents, Technical Efficacy Thesaurus, Application Domain, Technology Topic, Popular Technical Reports.
© 2025 PatSnap. All rights reserved.Legal|Privacy policy|Modern Slavery Act Transparency Statement|Sitemap|About US| Contact US: help@patsnap.com