Driving motor for automobile cooling fan
A technology for cooling fans and driving motors, which is applied in the direction of connection with control/driving circuits, electrical components, and electromechanical devices, etc., can solve the problems of difficult assembly, difficult to guarantee flatness, torque ripple, etc., to save welding positions, convenient The effect of stable welding and ensuring flatness
- Summary
- Abstract
- Description
- Claims
- Application Information
AI Technical Summary
Problems solved by technology
Method used
Image
Examples
Embodiment Construction
[0046] The present invention will be described in further detail below through specific examples.
[0047] Such as Figure 1 to Figure 13 As shown, a driving motor 100 for an automobile cooling fan includes a controller assembly 200 , a stator winding 300 and an outer rotor assembly 400 .
[0048] The controller assembly 200 includes a housing composed of a heat sink 1 and a rear end cover 2, a conductive support 11 and a PCBA board 8 are arranged inside the housing, a central shaft 4 is provided on the front of the heat sink 1, and the stator winding 300 is fixed on the front of the heat sink 1, the central shaft 4 is located at the center of the positioning winding, the outer rotor assembly 400 is rotatably mounted on the central shaft 4, and the heat sink 1 is provided with a capacitor installation area 102, an inductor installation Area 104, conductive bracket installation area 106, wire harness joint area 105 and heat conduction platform 101, described conductive bracket...
PUM
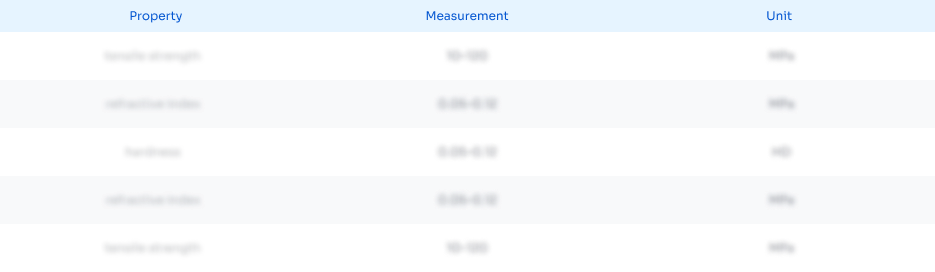
Abstract
Description
Claims
Application Information

- Generate Ideas
- Intellectual Property
- Life Sciences
- Materials
- Tech Scout
- Unparalleled Data Quality
- Higher Quality Content
- 60% Fewer Hallucinations
Browse by: Latest US Patents, China's latest patents, Technical Efficacy Thesaurus, Application Domain, Technology Topic, Popular Technical Reports.
© 2025 PatSnap. All rights reserved.Legal|Privacy policy|Modern Slavery Act Transparency Statement|Sitemap|About US| Contact US: help@patsnap.com